Been a long couple of weeks, haven't gotten much done on the car but have been busy otherwise. I've done snippets of work, much isn't worth showing but spent some time cleaning, scrubbing, and cleaning again. I wasn't worried about getting all the stains out, but focused on getting most of the crud off things.
This weekend I finally got some assembly done:
I had some cylinder shims made up. These were cut for me by Laser Equations, as I couldn't get any from Volvo and even then I couldn't get them thick enough. The cylinders are supposed to be shimmed .006-.008" out of the block, and Volvo sells (sold) shims in the range of .003-.006". My cylinders were all .002-.003" down in the block, and nobody talks about stacking shims so I assumed it was not to be done,and I had these cut out of .011" shim stock. I mic'd them and arranged them by average thickness, applied the thinnest to the one cylinder .002" down and the thickest to the cylinder on the deep side of .003" down. Two were spares. They ended up being cheaper than buying a dozen from Volvo that I was going to stack, were they available.
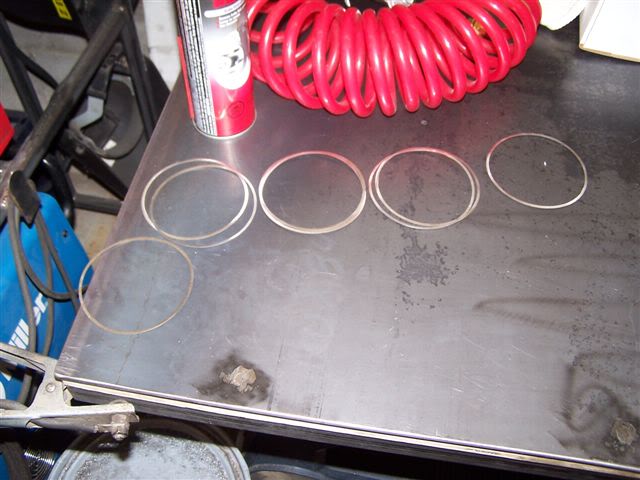
To seal them:
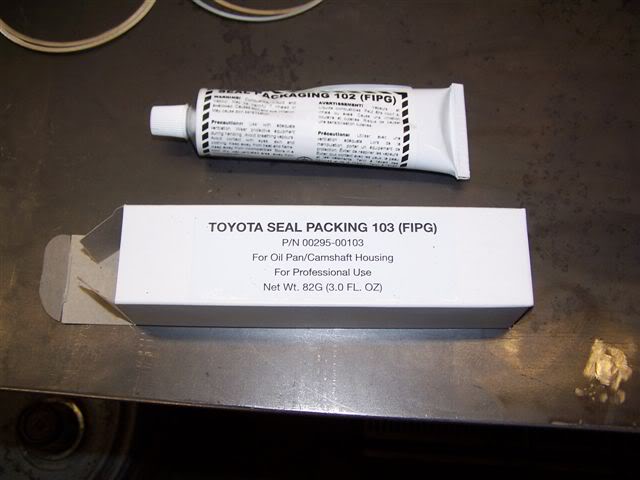
Clean head bolts and washers, plus some leftover thread lube from the evil V8-244 project.
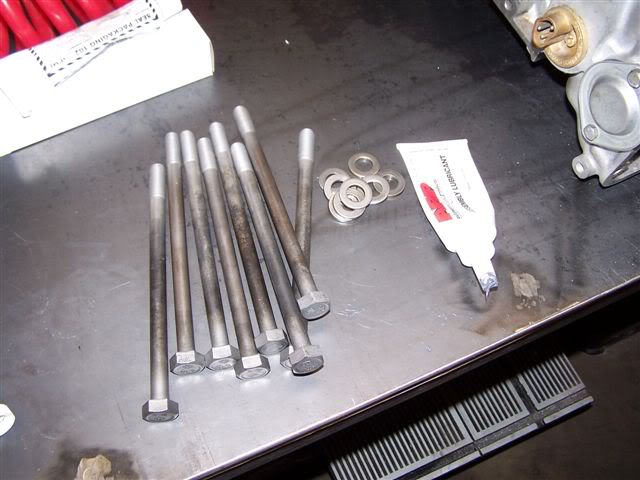
Order of assembly, step #1: install crankshaft. As the studs are long enough to go through the main caps and the cradle, and as the studs aren't threaded far enough to bolt the caps directly to the block, one is instructed to use 4 spacers to bolt down #1 and #4 main caps, while using the cross-bolts to hold #2  caps.
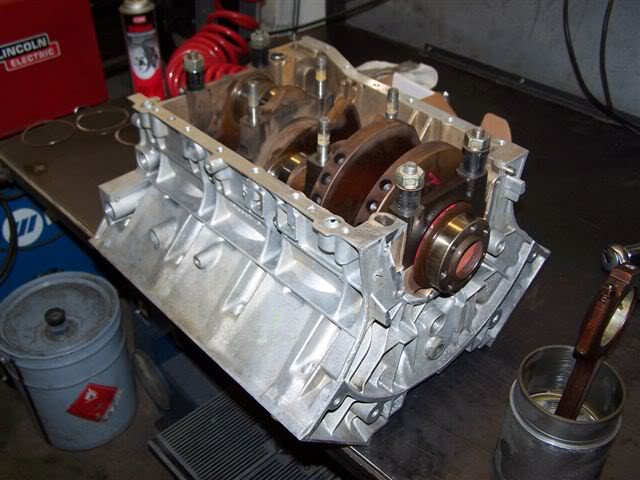
Step #2: prepare cylinders. I deviated quite a bit in the assembly procedures here. The factory says to install the cylinders, using cylinder hold-downs to keep them in place, then to install the pistons/rings in a conventional manner. I pre-assembled the pistons/rings into the cylinders and set them aside, marking the location of the major thrust axis (and therefore the ring gaps, another deviation of mine). I then laid a bead of sealant, installed a shim, added a second bead of sealant, and smeared assembly lube on the bearings.
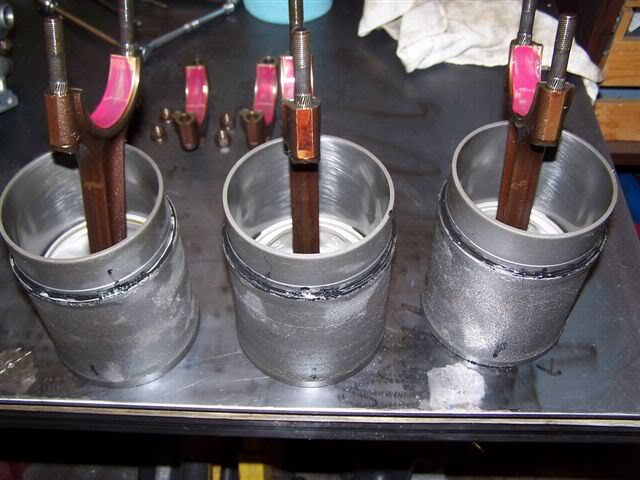
A close up to show the source of a heart attack to come later.
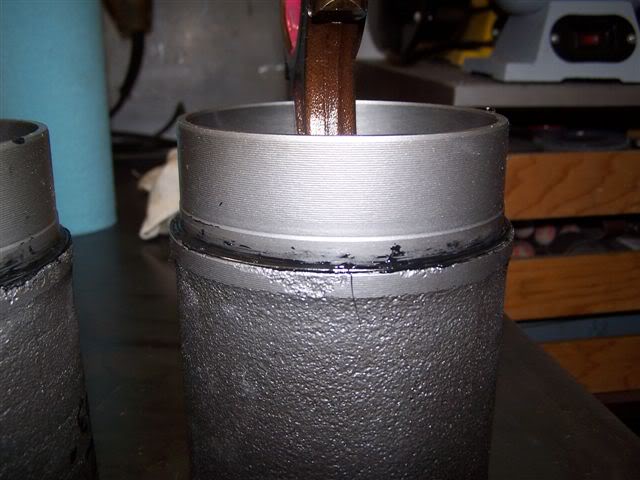
One side done. Hurry before the sealant hardens!
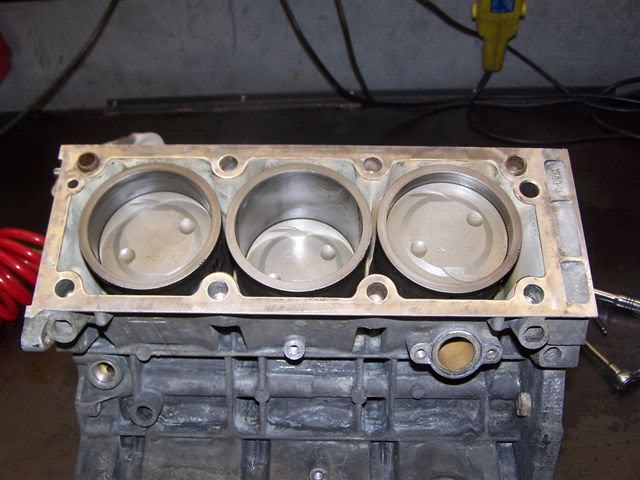
Head on and torqued to the first stage, to squish out the sealant and seat the cylinders in the block. Another reason for my deviation to the assembly steps was because I wasn't sure what sealants (if any) were on the factory shims, but I knew I would be using the Toyota goop so I would want to seat the cylinders into the block evenly and with authority, and using the head was the best way I could think to do this.
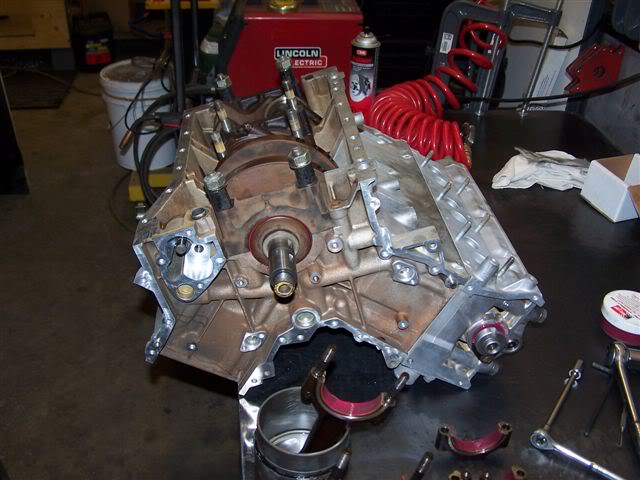
Repeat steps for second bank:
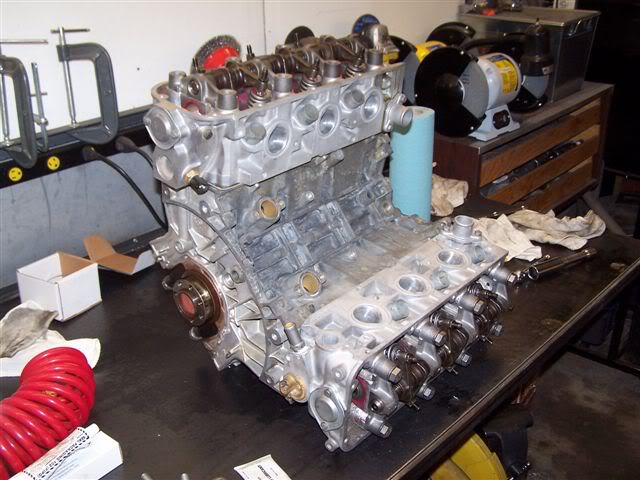
Oil and torque rod bolts to spec, and bust out more expensive chemical gasket:
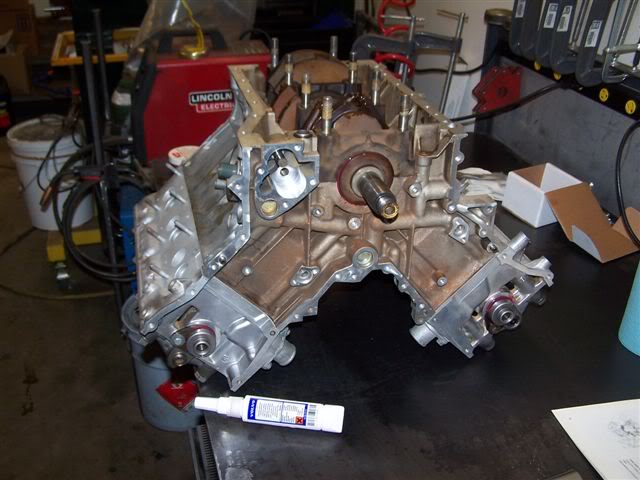
Smear the delightfully pink Volvo goop all over everything (block rails and rod caps). Don't forget the oil pump O-ring (I didn't):
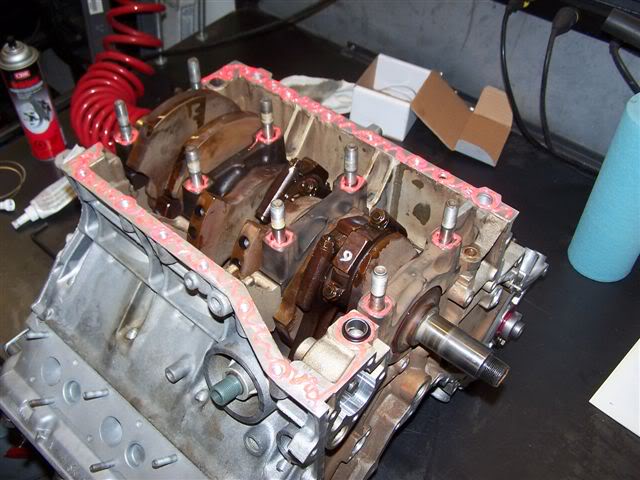
Don't forget the rear main housing (I did, at first) and assemble. Use more sealant on the "outside" 4 main bolt washers and torque to spec, and bolt up the perimeter bolts, locking the cradle to the block.

It is at this point that I realized something important: I hadn't been overly careful seating the thrust bearing and making sure the rear thrust surfaces were flush. I'm not pulling anything apart now - I will live with it. It's not a racing engine, and it's only got a torque converter pushing forward on the crank. It'll be fine.
Now for my heart attack: After it was all buttoned up and I flipped the block over, to install the oil galley threaded plugs & give things the once-over, I had a bit of a scare. Directly above the rear two (#1 and #4) cylinders there are large holes into the water jacket, and through one of these holes I saw what appeared to be a hairline crack. Even with a flashlight and my calibrated eye I was convinced it was a crack. While I was gooping up the shims the connecting rod shifted and once I half-dropped a cylinder assembly, bouncing it off the steel table. A couple other times the rod dinked off the cylinder while shifting things around. Could I have cracked the cylinder while doing this? Was the crack there and I missed it while blasting/cleaning/examining, and it only shows up when the head is torqued on? Was this why compression was leaking into the cooling system? Will I be installing the redblock after all?
Then I reached in with a pick and scraped the little stringer of sealant goop off.
