I thought this engine was worth having a look at and kick around in the forum. I've seen inside more pushrod engines than I care to talk about, but this situation was new. In the summer I was assisting Jim (Woodenshoes) tuning his 122S and noticed that when he cranked the engine, the crank pulley moved quite a lot.
https://youtu.be/5GAhyM8ZZfkThe video is how Matt and I sometimes communicate - ha, ha. Now every engine I build I check the thrust clearance and they have to be very tight (like 1 - 2 thou tight) - not visibly moving. There were also issues with tuning this engine as the carbs (fresh rebuilds) wouldn't play nice. Now, this engine was one of the big buying points for Jim for this car. It was supposedly full of all the best stuff IPD has (dual valve springs, HD oil pump, header, VV17 cam, high rev kit (Chevy lifters and longer pushrods)) - you get the idea. Hot stuff and just being rebuilt it looked like a winner as I would charge almost what Jim paid for the car to rebuild the engine to this specification.
The first time I drove it, Jim wanted to know if it had similar power to my 122 with the B20 - my blunt answer was NOPE. It's hard to diagnose why - the engine seemed happy enough, but there wasn't much snap to it. It should have been better - we thought it was carbs and tune related. After seeing that thrust bearing - I was suspect of the rebuild.
So fast forward about 6 months and we're pulling the engine.
With a rented engine hoist large enough to yank a tractor motor...we pulled the engine out this week. Things were not looking good when I pulled the transmission off and the pilot bearing fell on the floor. No one had installed the oil slinger or the clip. Not really a great sign of the care and attention to detail needed when assembling engines.
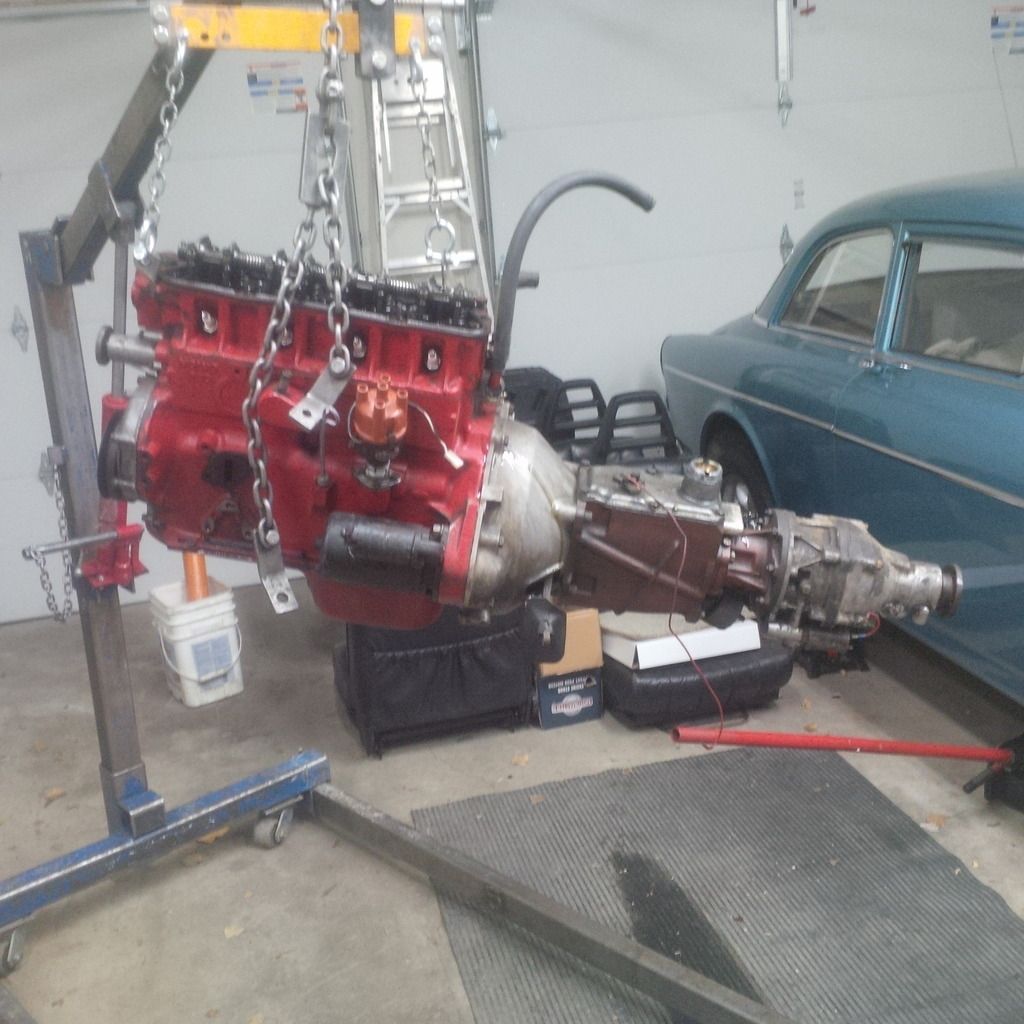
Then with the head pulled, we can see that cylinder 3 - 4 were along for the ride. 1 and 2 look like they were running fine.
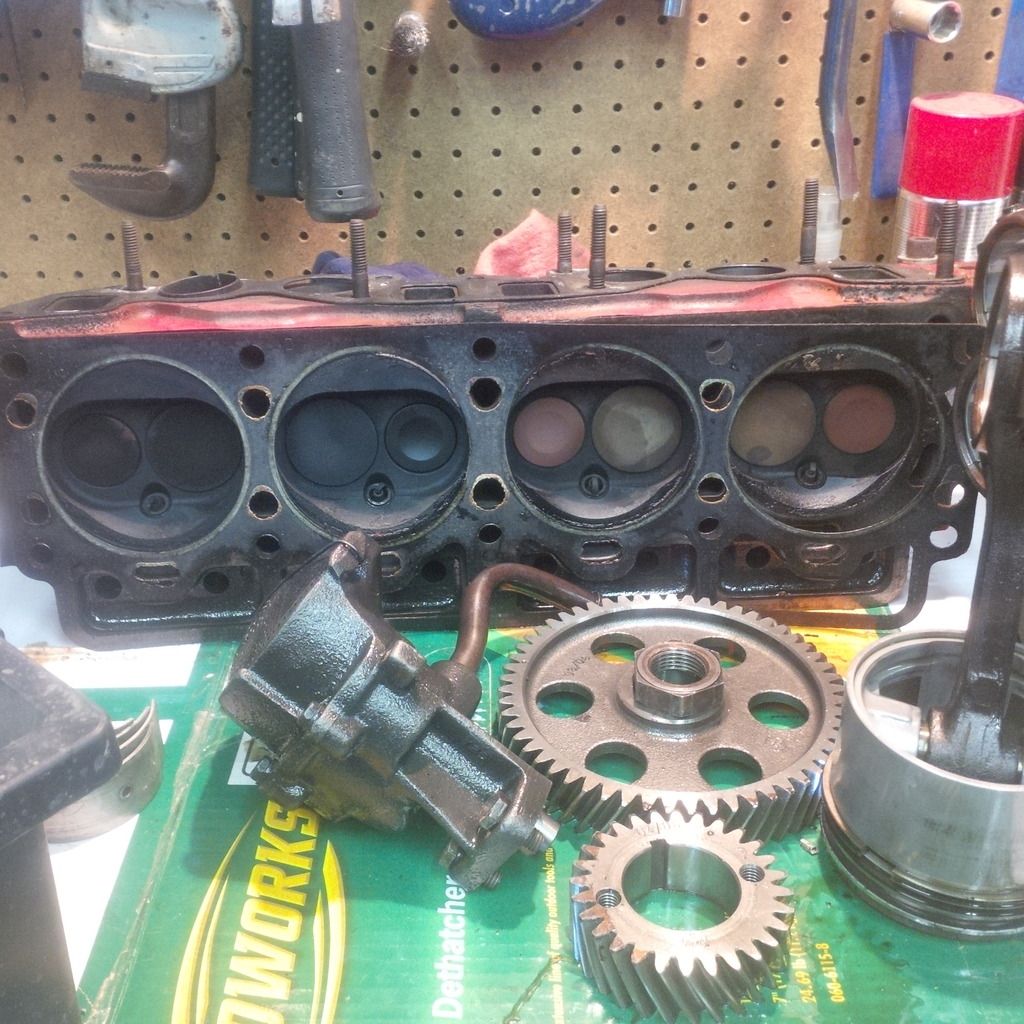
It did have new Mahle pistons and steel timing gears and the HD oil pump so at least the basic parts are sound. 3 - 4 exhaust valves are recessed inside the head (the valve margin is level with the head or inside the head). So the exhaust seats are done but the valves are new as are the guides and it does have the double valve springs/high rev kit. So new valves and seats are needed. These issues were also confirmed by the lack of compression on 3 - the valves were leaking. So running on 2 cylinders in essence.
Next we whipped out the pistons and found that the lack of thrust bearing had caused wear in the bores in line with the cylinders. They usually only wear perpendicular to the main line of the block. It was easy to see, hard to photograph. What we saw was the "back" of the cylinder had deep cross hatch from honing evident and the front had almost none.
Back
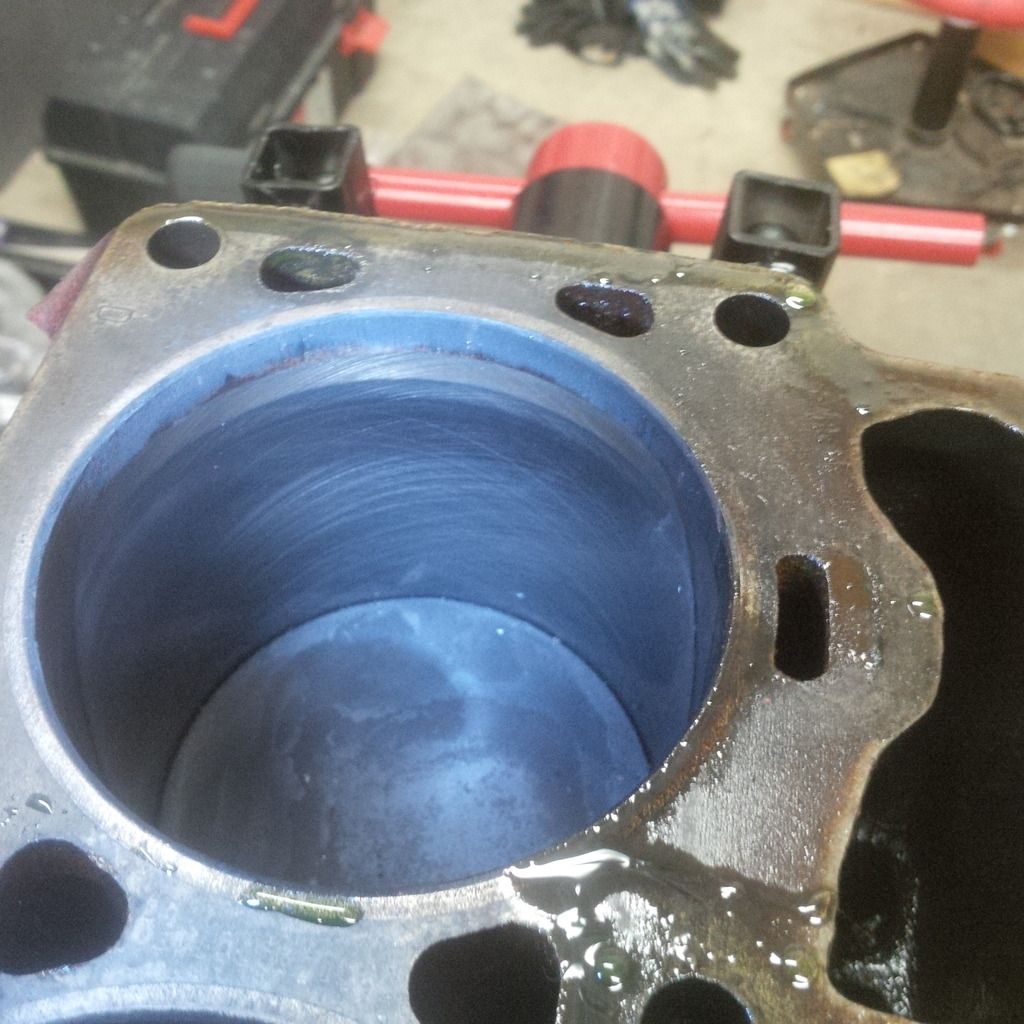
Front - you could see some hone marks with the flash light, but almost non to the naked eye.
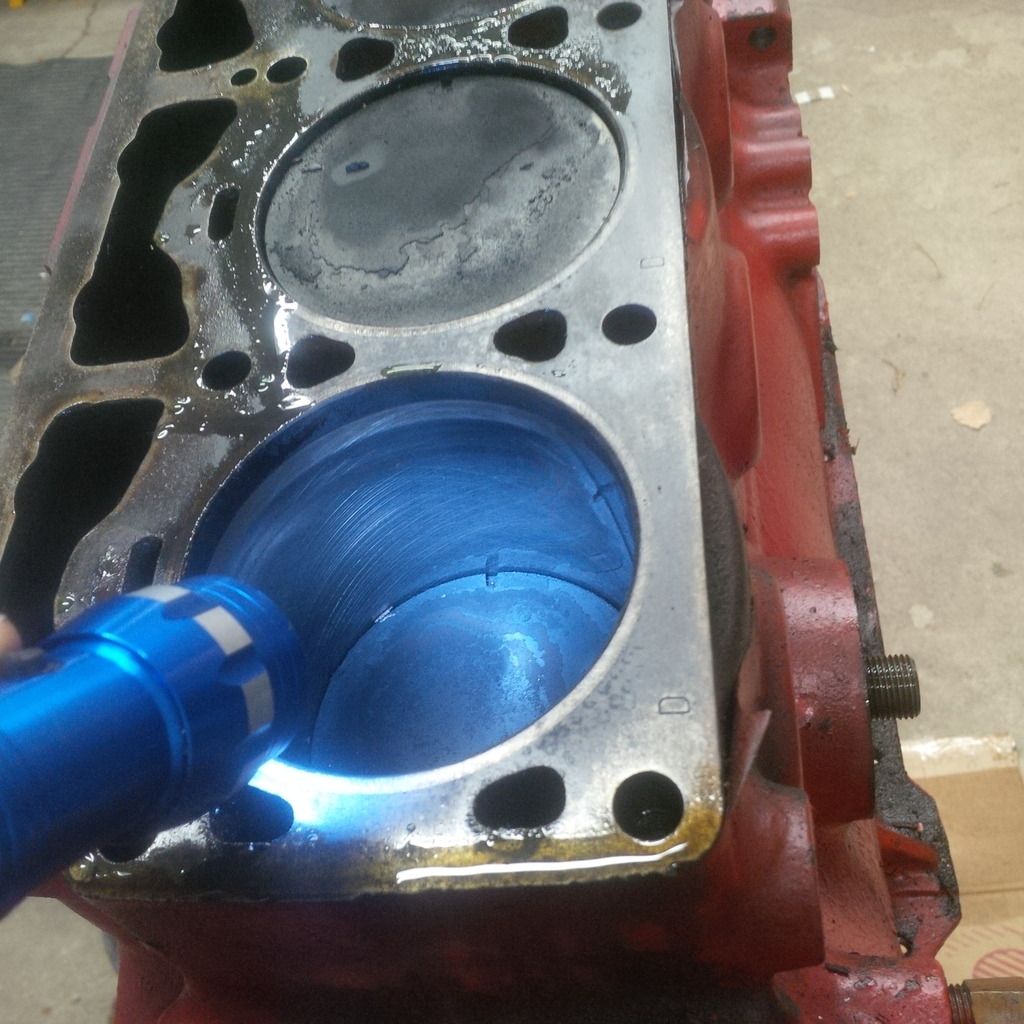
Flipped the engine over and found...horrors.
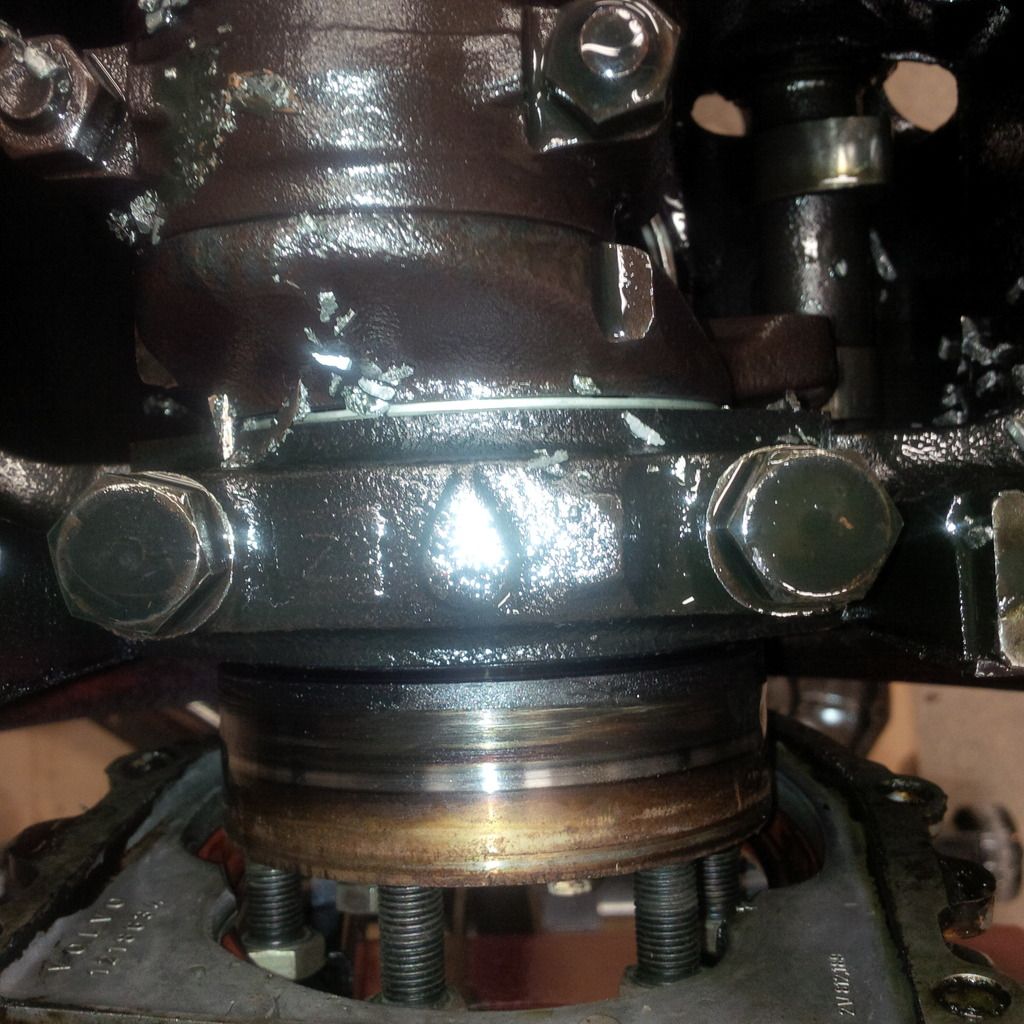
Those fragments are thrust bearing material. You can see that the bearing is missing from the rear of the #5 main bearing shell.
So out comes the pistons and crank. Yikes - this isn't good news.
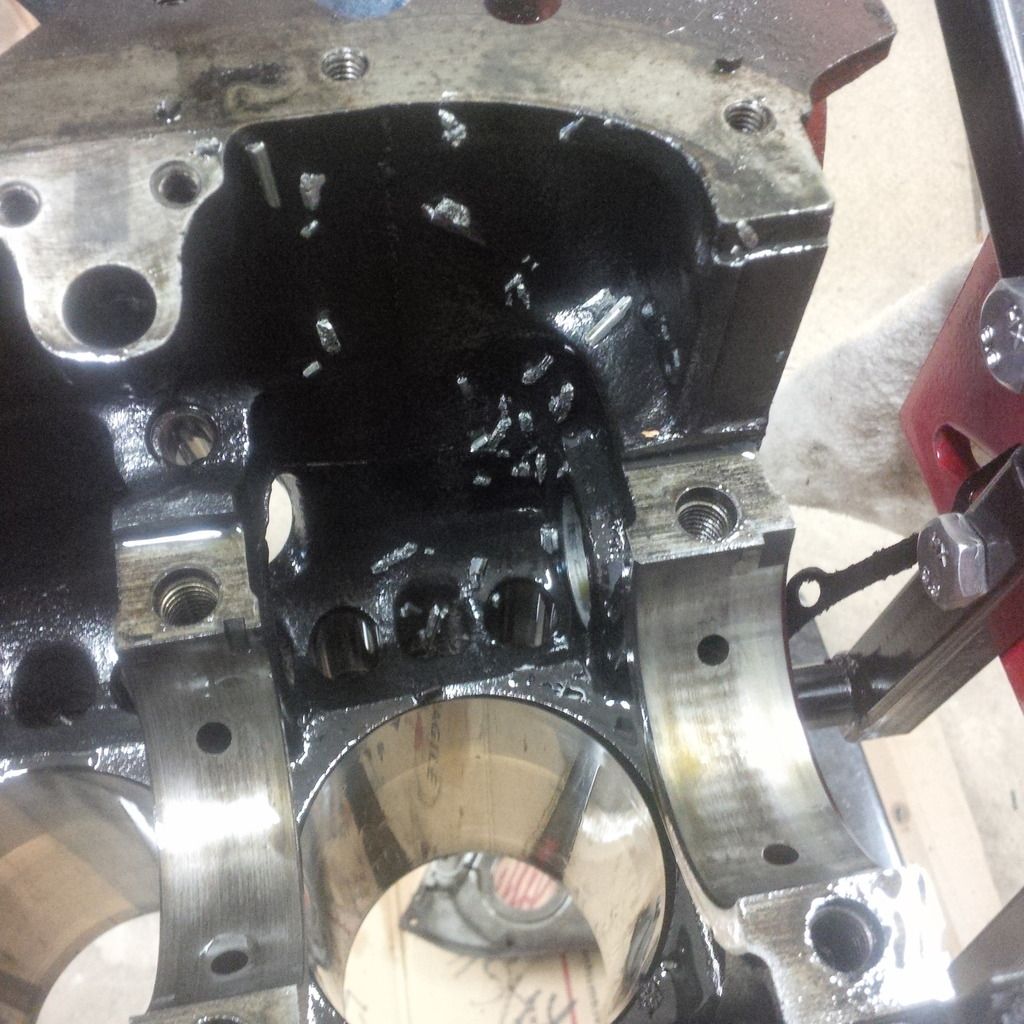
Some bearing material has gotten itself embedded in the rod bearings - they're now junk.
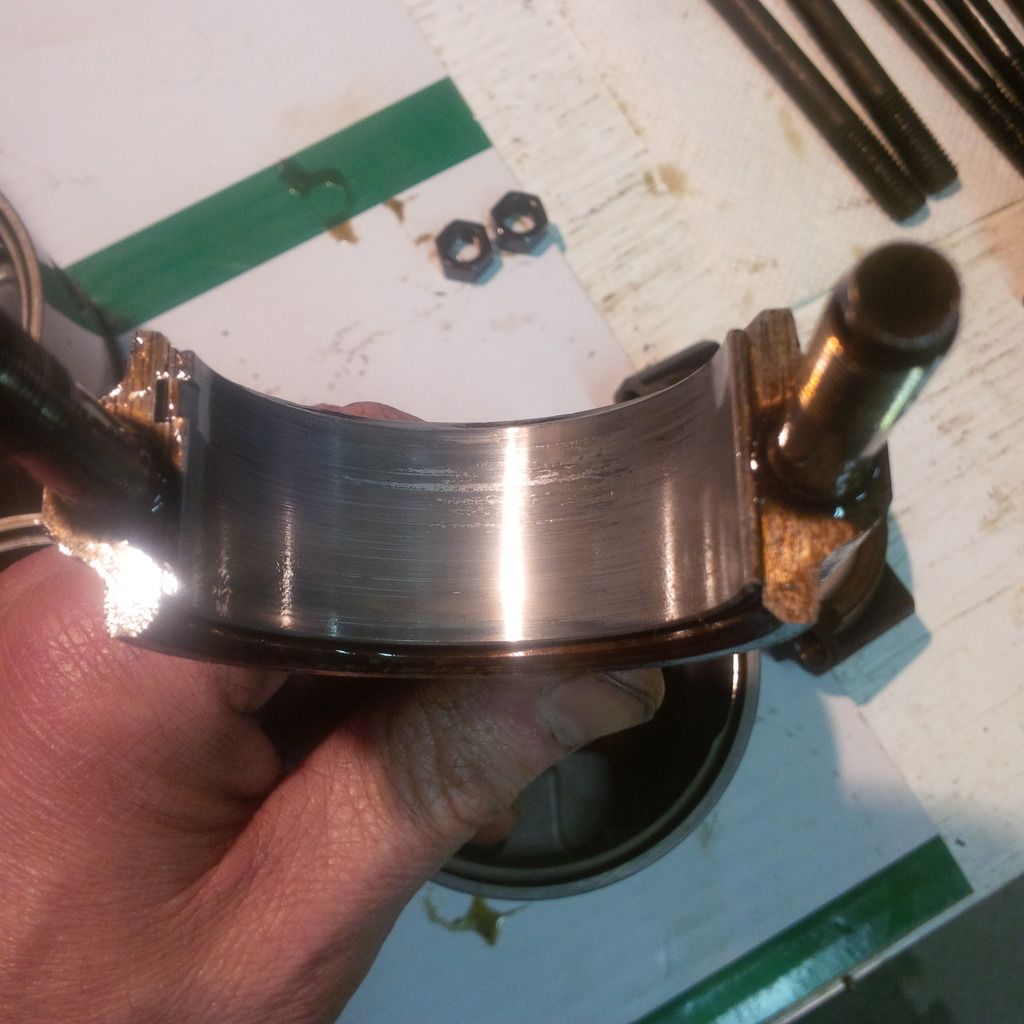
This is the wear on the thrust journal. Not sure if this can be welded and repaired, or if Jim's looking for a new crank.
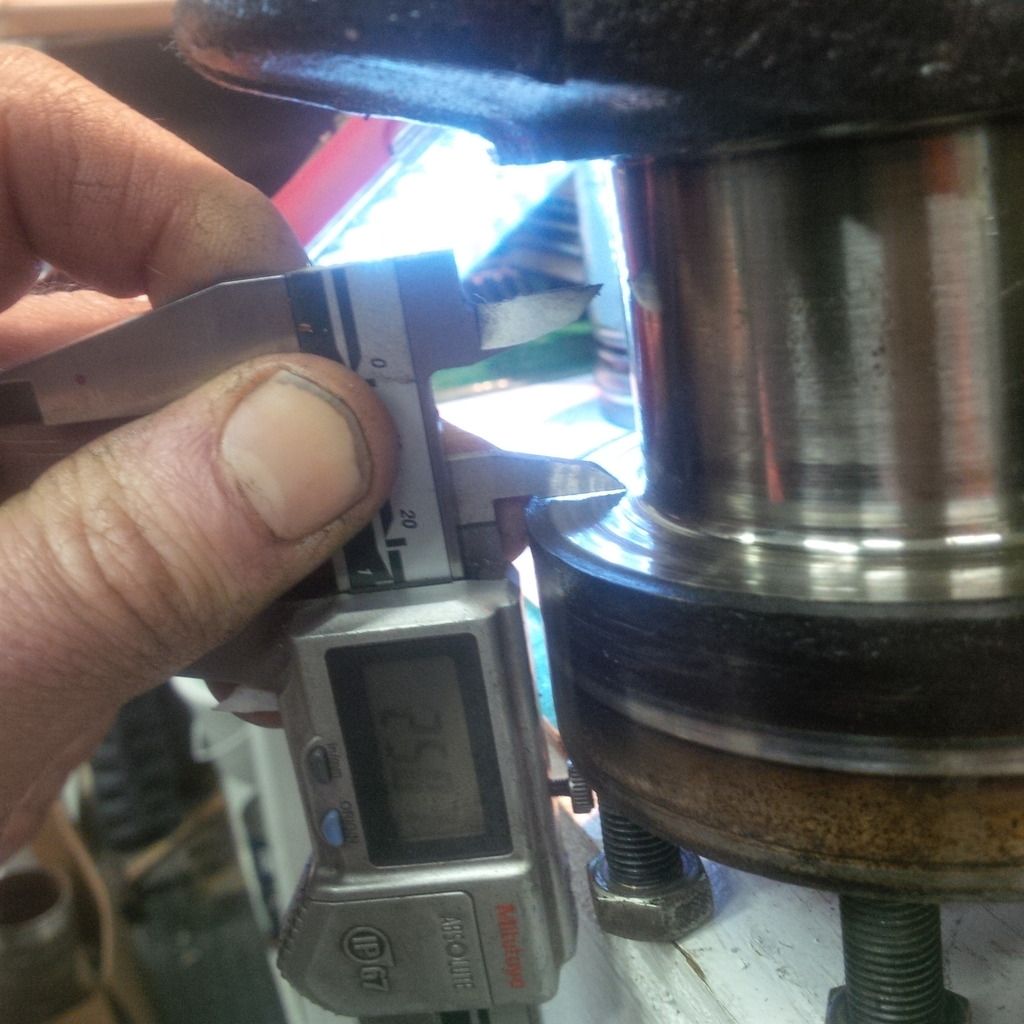
So that's the tear down. Here's my analysis. First, the thrust bearing is often overlooked when reconditioning a crank or when enthusiasts are building an engine. It's critical - just like all engine parts. Then the question "How did this happen?" must be asked. My first observation was that while the engine had been rebuilt, corners were cut. The block of the deck wasn't cleaned up (they are normally wavy and need at least a fresh gasket surface to mate to) and one of the head bolts was rusted (slight HG leak). The fasteners on the engine were loose...like the rear main seal was on finger tight. So we're dealing with some hack job rebuild.
The main line was bored but there was no hatch as you would expect from a proper honing. I don't normally hone the main line as these deep skirted blocks rarely come out of line and if you don't need to touch the factory work, I don't. So someone thought this was a Chevy V8 and line bored the block - no hone. This, in my analysis is how the bearing went bang.
The thrust bearing is present to ensure that thrust loads are contained, if the main line is not perfectly perpendicular to the bores, then the thrust bearing is placed under undue load. They can also fail due to excessively coarse surface finish (a reground crank with spiral finish on the thrust face is not good as the groves wipe the oil from the bearing and cause failure) - but Jim's crank is standard size, so that's not the issue. I'm willing to bet that the main was bored a little crooked. These things should never need boring - just a hone (I've done only one ever) - a few thou is removed from the caps, they are replaced and a line hone is run though the engine to hone it to size.
The block is salvageable with a light deglaze and deep clean (it was very dirty) we're ready to go. Then with new valves and seats the rest is fine. So a top and bottom gasket set, new cam (it was on it's way to wiped) and hopefully a new crank and this one can be buttoned back up and be ready for the driving season.