It's no secret that the P1800/1800S/1800E have an Achilles heal; the shock tower on the front suspension is prone to stress cracks. This is so common that IPD suggests reinforcing the top of the shock tower if you're buying Bilstien shocks. The visually similar crossmember for the 122 is not as prone to this problem as it is fabricated with slightly thicker material. I've seen other "How-To's" on the internet, but thought I would share my latest repair…which was a doozy.
In my opinion, this problem is partially caused by the material and partly because of the limited travel of this suspension design. The car in question came from Regina, SK - a city not renowned for it's glass smooth roadways. I suspect that years of pounding on the Saskatchewan roads were responsible and that the odd pot hole at speed was more than enough to require the initial "repair".
The crossmember is completely removable if you remove the 6 bolts attaching it to the frame and remove the end links and the brake and clutch lines. A little help from a pry bar and the clip comes out and is ready for repair. Please don't attempt to repair this sort of damage with the parts on the car - this is your safety at stake. Also DON'T DO THIS IF YOU ARE NOT CONFIDENT IN YOUR WELDING. If you can "stick" things together with weld - suck it up and take it to a professional (or someone that plays one on the internet

).
Once out you can fully inspect the complete suspension for other problems (lower control arm mounts - especially the rear and the mount for the sway bar are known issues as well).
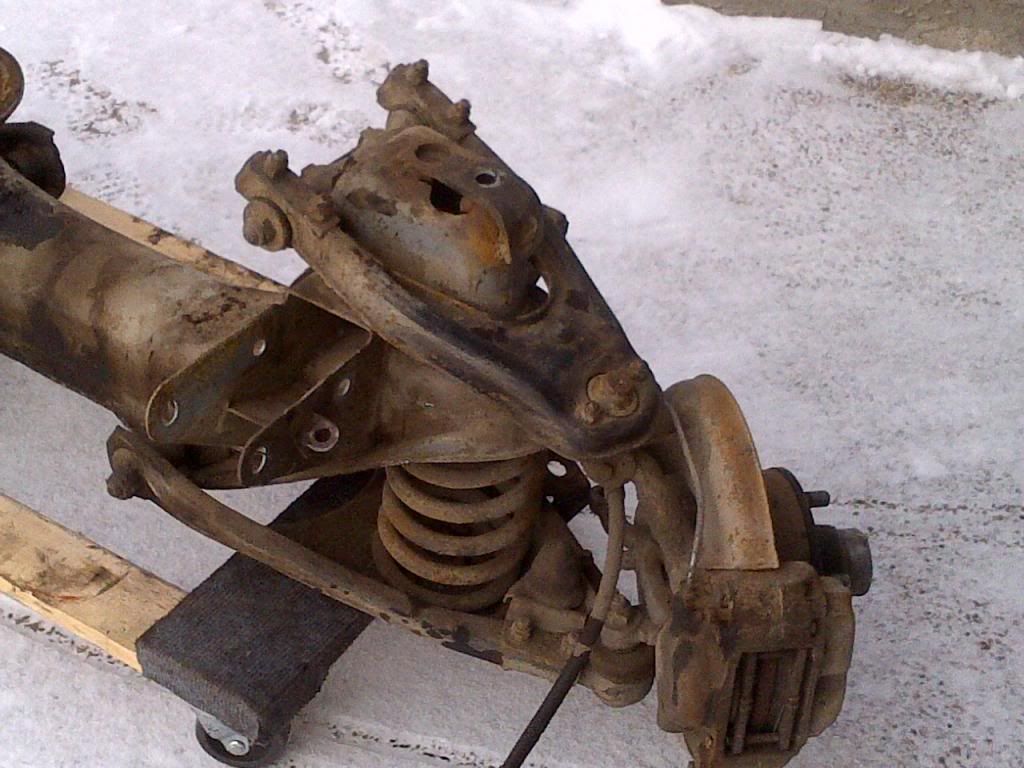
Here you can see the sort of repair I see all the time on these cars. Someone found a piece of 1/4" steel flat bar and figured this was a good way to repair a very badly damaged shock tower. Nasty. The holes were probably in the steel strap before and were partially welded - not the way a button weld should be executed.
Close up. This is the worst damage I've ever seen on one of these…and I drove this car…on a highway…at speed...
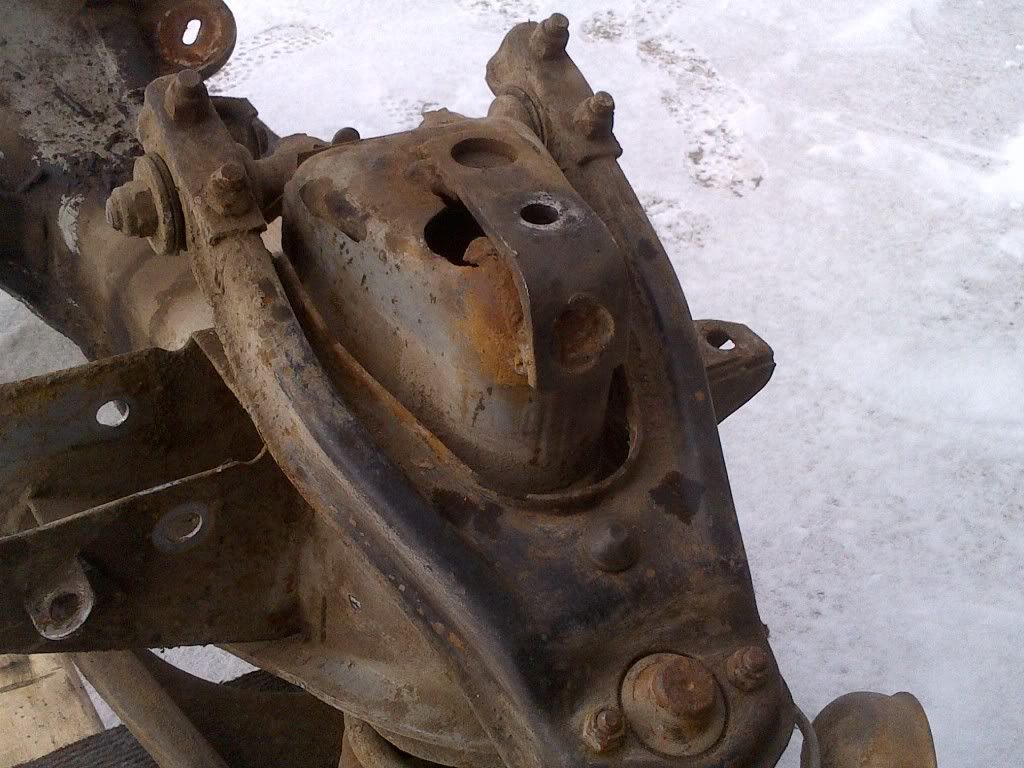
Nice to see that the shock was centred...
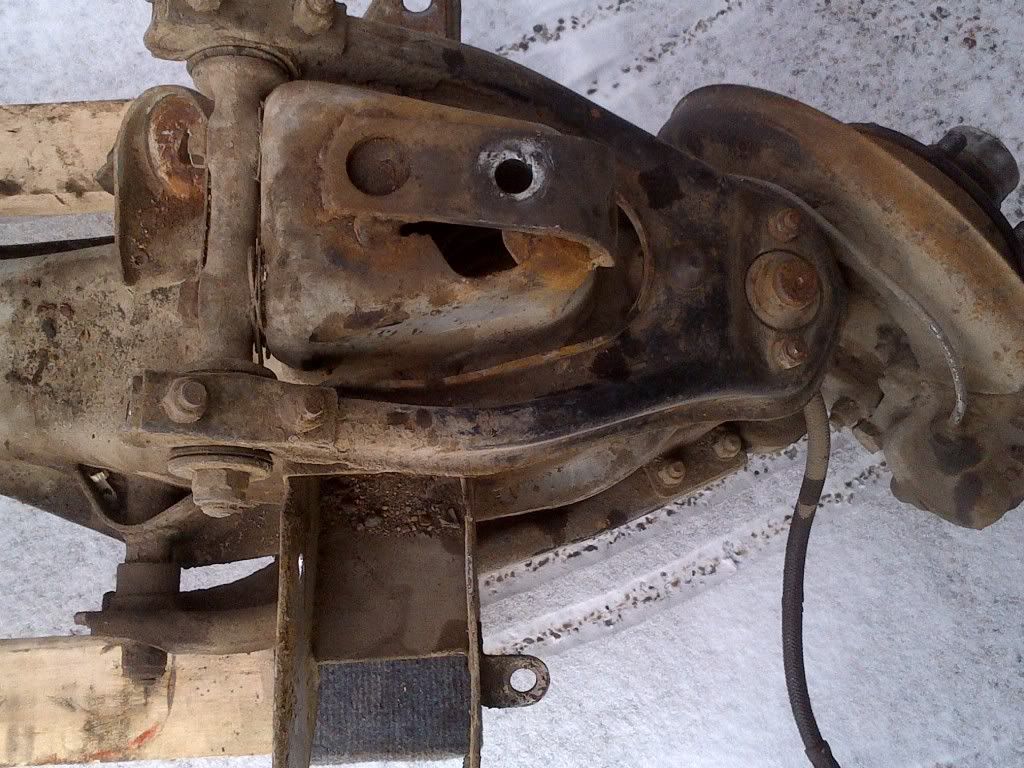
A very heavy coat of undercoating was applied to the other side of the crossmember. It was, of course, hiding a cracked tower as well. Not as bad as the other side, but undercoating - no matter how thickly applied, is not structural people. Be careful when buying these cars - ethics is not a used car seller's strong suit. A few minutes with a wire wheel exposes the damage.
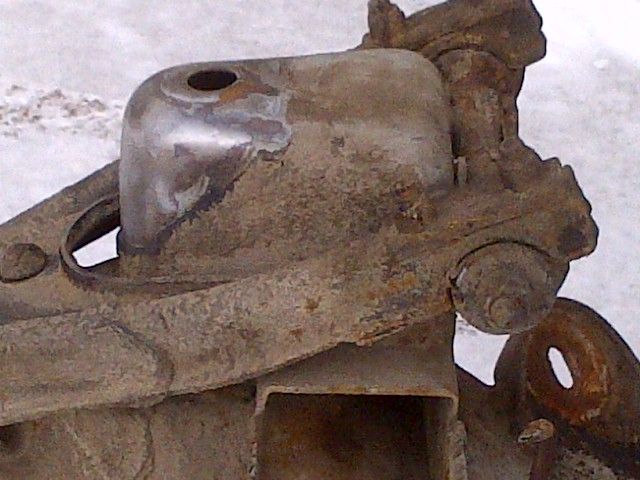
This assembly is being completely rebuilt and powder coated, so here it is stripped of all parts. Have a look at those welds…they are COLD and look like someone with the shakes did them (maybe Grandpa?).
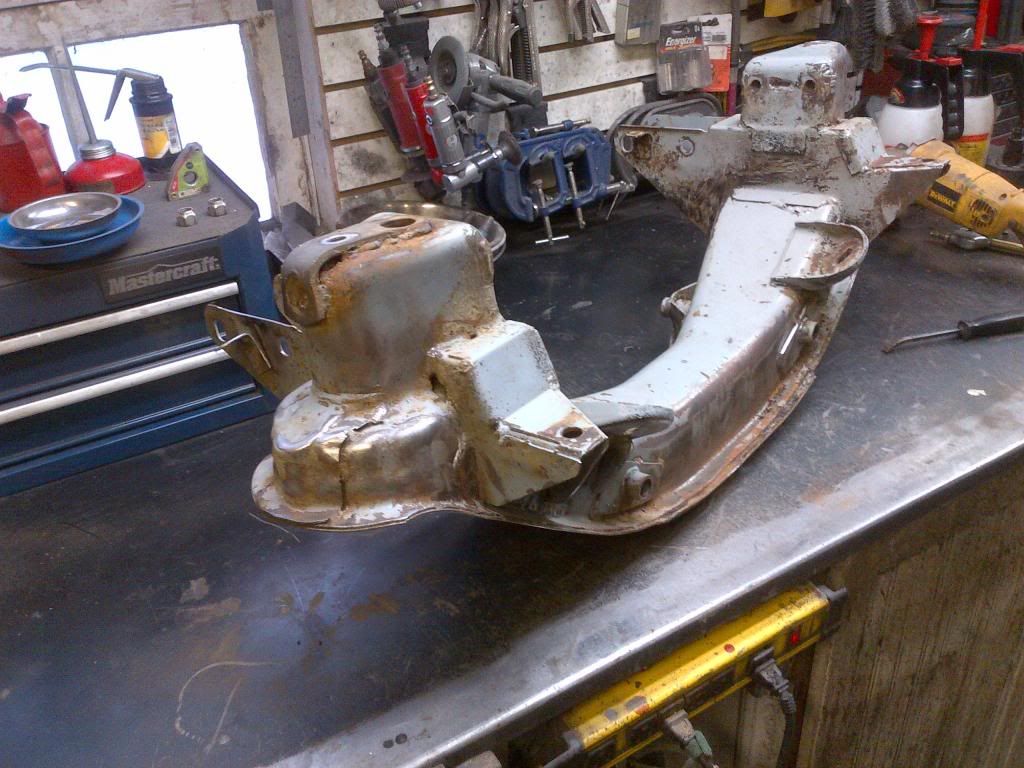
I carefully removed the strap and revealed the state of the tower prior to repair. I'd like to beat the guy that "fixed" this senseless - honestly - who does this? Could have killed someone.
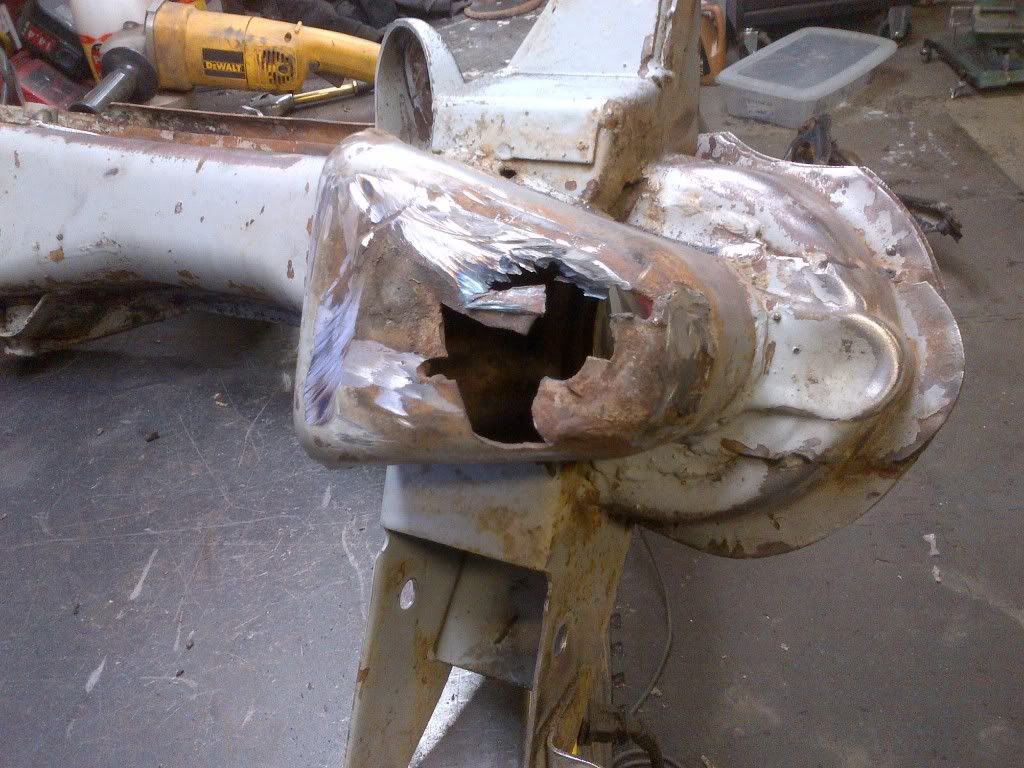
Now when metal looks like the above picture, it's not a good idea to just gob some weld on it and assume it's going to be OK. It's fatigued and fractured. I cut it all off and fabricated a cap for the front damaged area from 10 gauge steel. Here's the end result. That's a real repair.
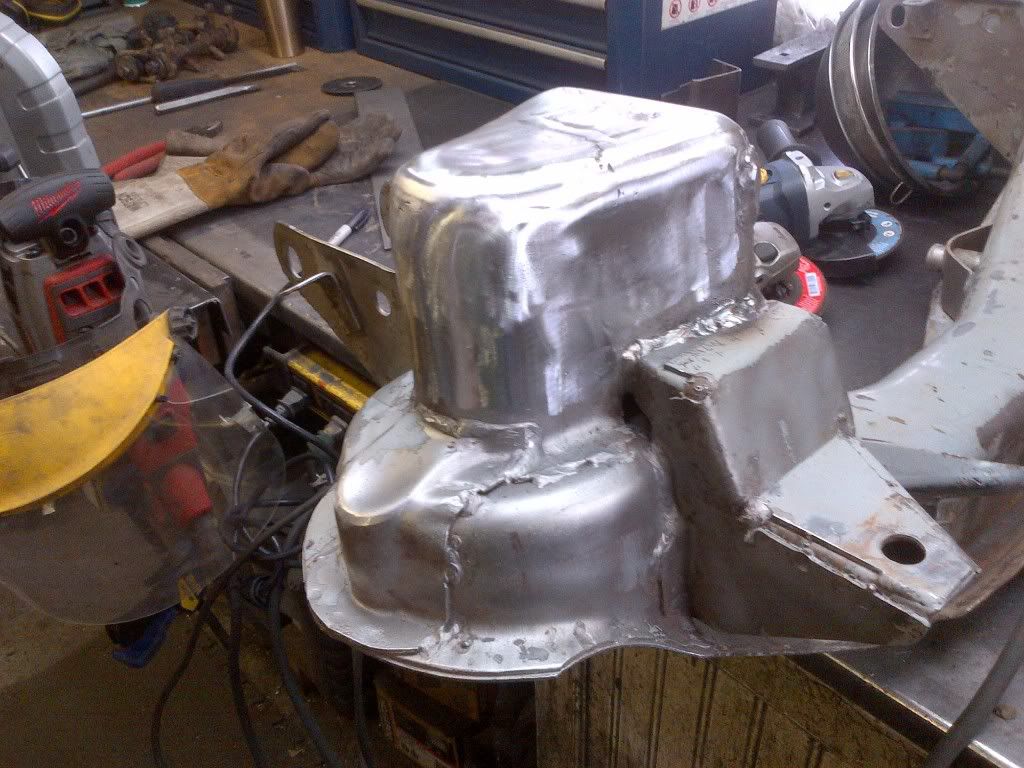
Here it is from below - note that the welds are 100% penetration welds. This is what it should look like.
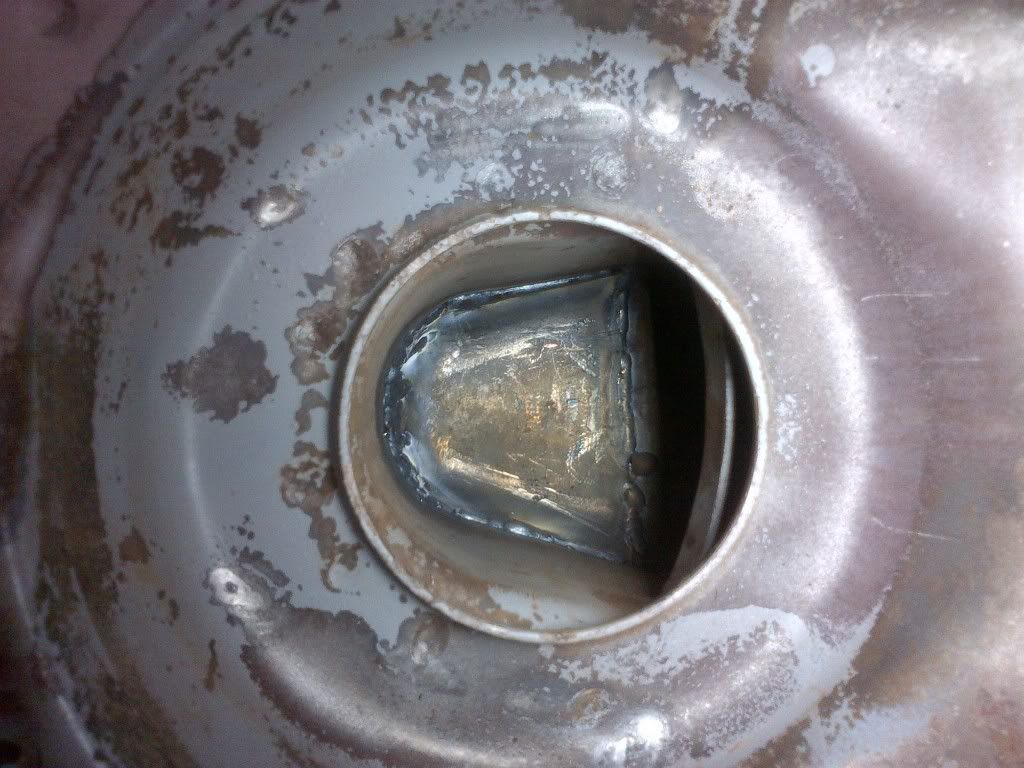
3/16" steel reinforcement plates were fabricated and TIG welded. A perimeter weld was all that was required for a proper repair in this case. It's not going anywhere - could have used 10 gauge.
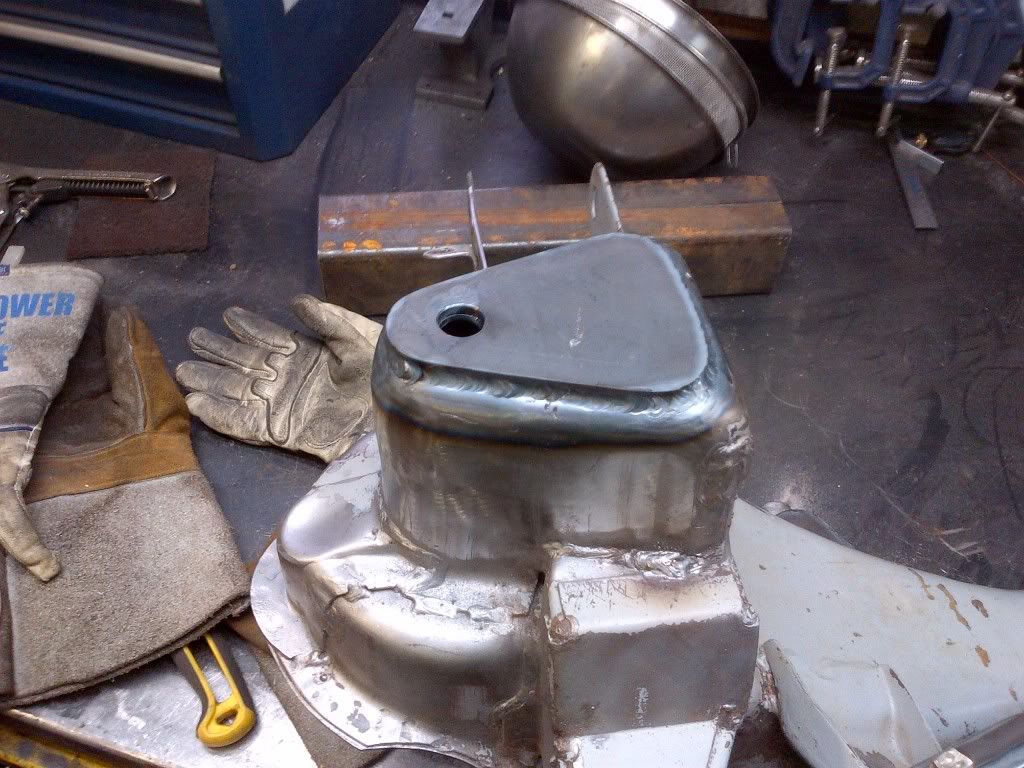
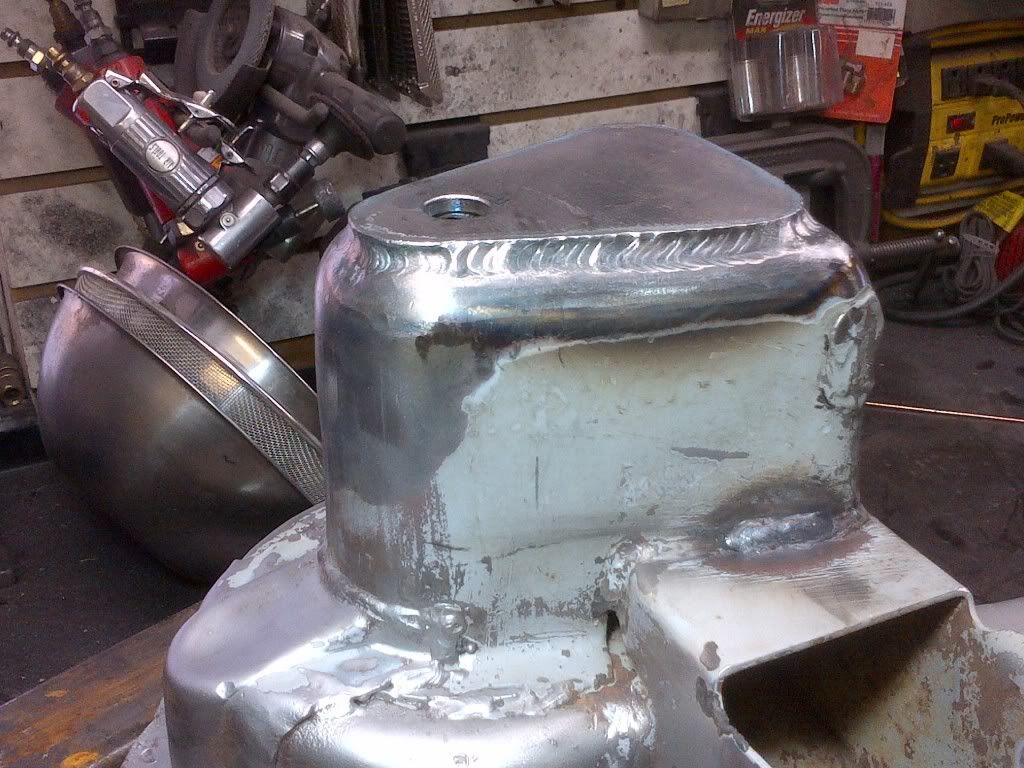
The lower control arm rear mount is often cracked on these cars. The welds on this crossmember were incomplete around the tube towards the bottom. These were stick or flux-core welded back in the day and the welding slag was still in place. It's not structural either. The weld looked complete, but wasn't upon close inspection. This mount sees a lot of torque during braking. I'm guessing this is why they crack - they weren't welded properly.
I welded it up and then capped the top. This cap significantly enhances the strength of this single-shear joint. Nothing wrong with more strength. All TIG welded.
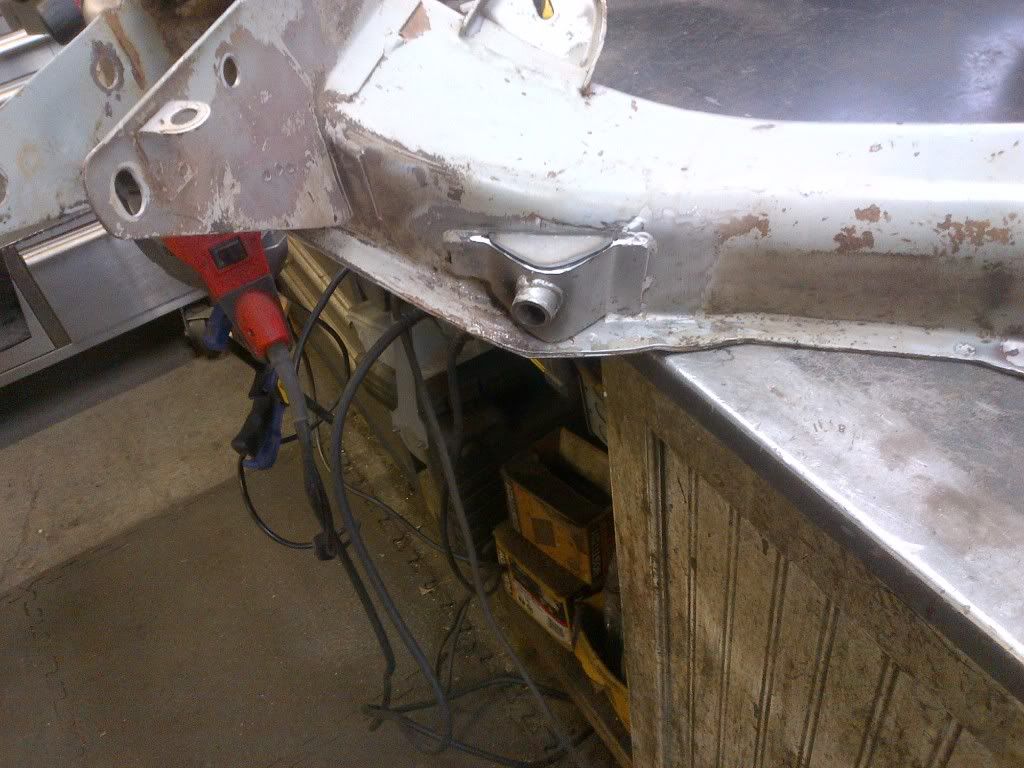
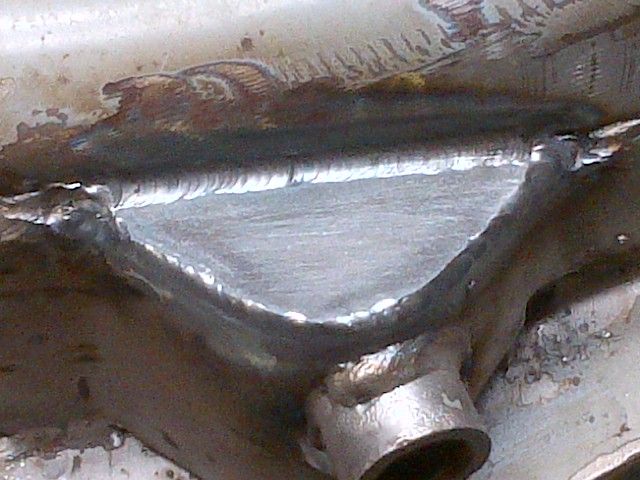
The sway bar mount can crack from the use of the large IPD sway bar or suspension bottoming out. This one was fine - but I'll show you what I have done. The bottom of the mount has two really small tabs welded, then a little more at the top. Nothing wrong with this in theory - probably just fine for the original sway bar. I added a stiffening plate and welded up the sides. There is more that could be done to stiffen the arm, but this isn't a race car.
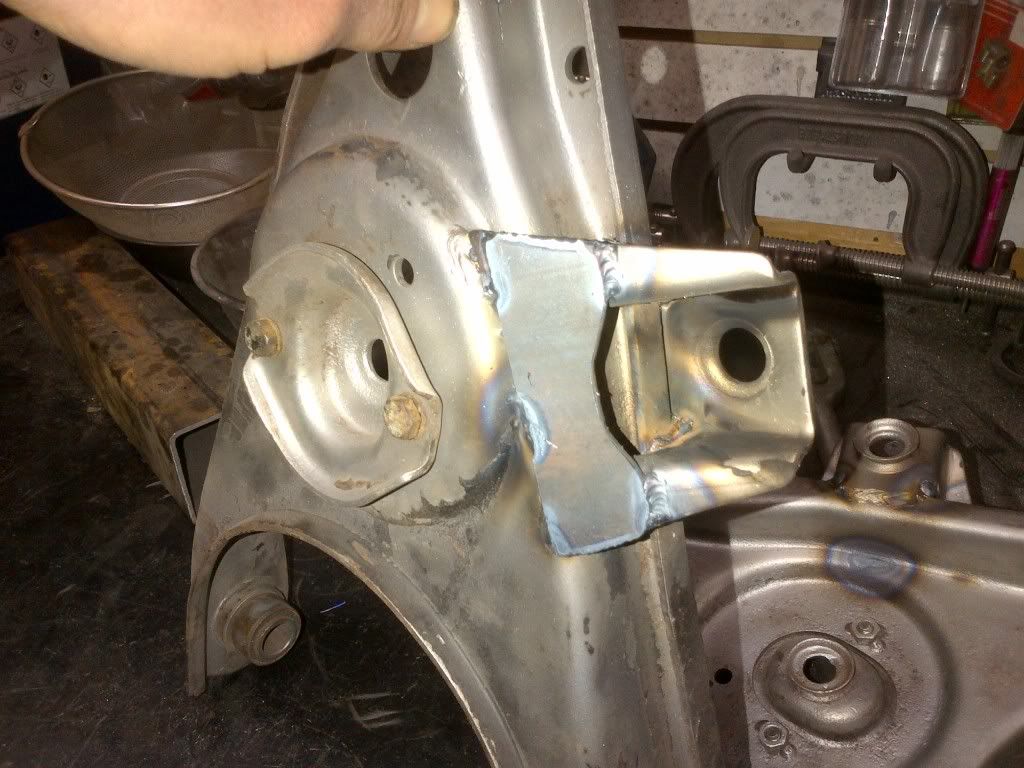
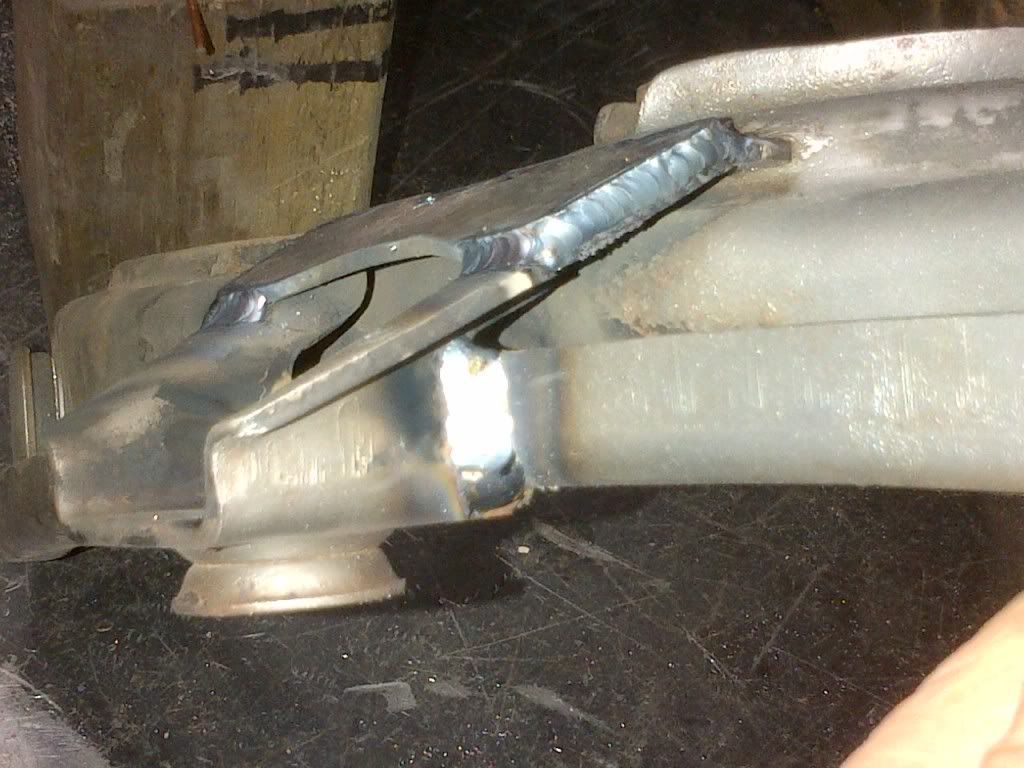
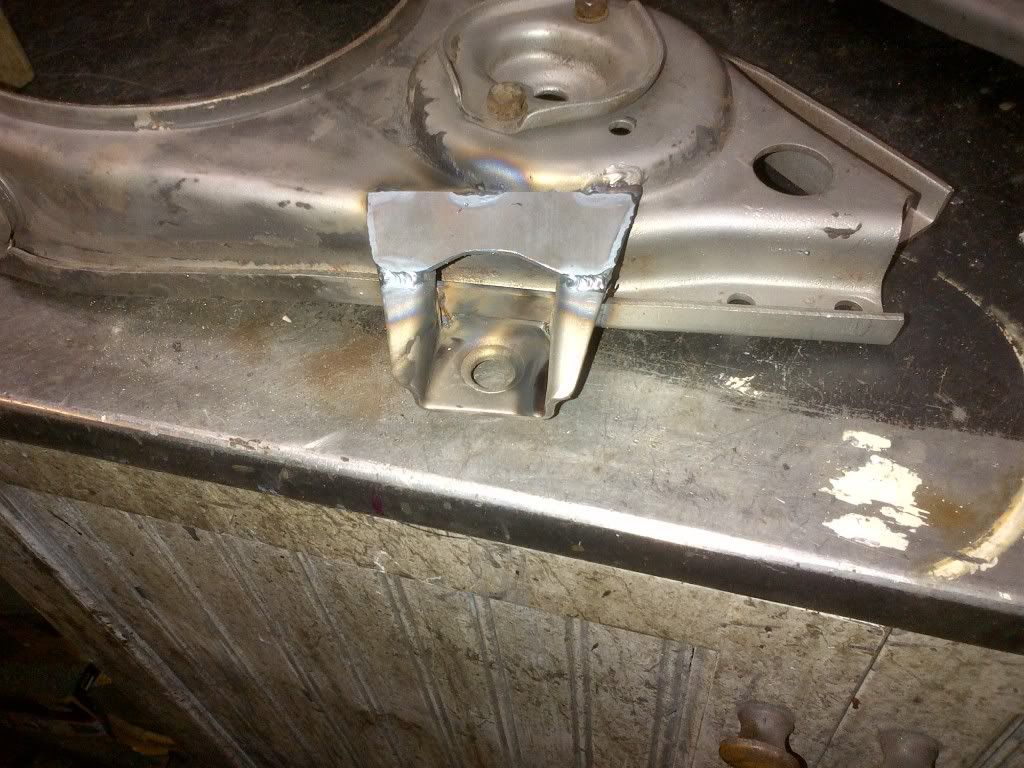
There you have it. Next shots when it's all powdered and pretty.