We left off with the following done:
I had fabricated these diagonal parts to further strengthen the K member.

Clearance is just what I was after - so I'm happy (a rare emotion in the last month).

But I ended the episode by saying that I wasn't going to pull the frame to weld it all up until I was done with the details. You'll always miss a few details in a build, but I do try to get things wrapped up in a more orderly fashion these days. So there were/are a million things to address.
The first was to actually get this frame perfectly centred. Now, when it went in before, the outriggers to the A pillar were keeping the frame from squaring perfectly. It was 1/16" but it would have kept me up at night. So I had to hack the end of them off. Recall, I made these parts - you can jack the car on them - but they should have been installed once the main rails were squared not before - my bad.
Here's the before.

And after - dead on 12.5":

Now the outriggers are a little short (the plasma will do that). So I fabricated these extensions because I don't believe in gobby nasty MIG welds. They fit up inside the outrigger and slide out to the sill.

Then this happened...

My "Made in the USA" Quincy QT-54 - 50,000 hour compressor pump took an epic dump. FFS - I can't work without air. It filled the garage with an oily mess that landed on top of my already dusty nightmare.
So I had to ditch that junk (probably 2000 hours on the pump by the way - so about 48,000 short of the promise. The pump is made in China - go figure).
This meant a weekend was killed cleaning stuff and getting the new Rolair Chinook K28 (made in Italy - you can tell by the care taken with the paint - LOL) industrial pump.

Somewhere in all of this, the ARB brackets got welded.

Then when waiting for parts and the snow to melt, I started finishing off the details - like where is the plumbing going. That meant I had to find my spare bell housing, hydro throw out bearing, adapter and trans snout. The lines have to go somewhere. Then there was waiting for the brake lines to come in.
The All Star off the shelf brackets to hold these lines didn't fit the damn clips - seriously - I tried folks. Takes time to build your own brackets. but here they are.

I've also designed my own line clamps - doesn't take 5 minutes.
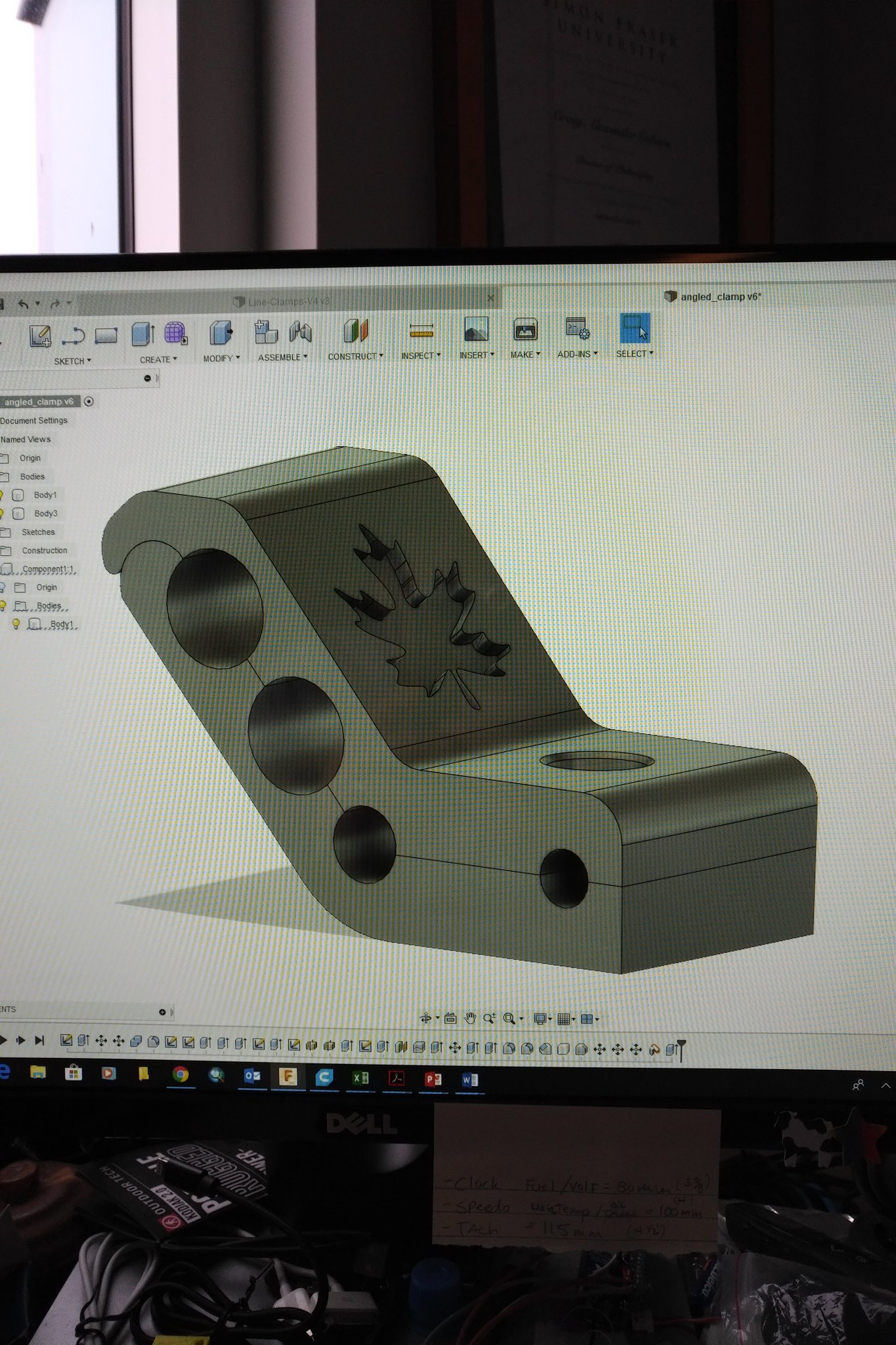
Had to do them for every possible line combination that I think I'll have under this car. That one fits along the rear seat pan.

These are just the prototypes - so not 3D printed with a lot of care or resolution.

You get the idea. Next, I wanted to epoxy fill the leaf motif. Worked pretty well.


The leaf is from the original "Made in Canada" Volvo badge. You'll be seeing it again on this build.
So today I put my garage back together and am just getting ready to pull that frame and weld it up.
Mic drop update?
I also developed a little merch - if anyone is interested.

[url="https://teespring.com/en-GB/throttle-stop-garage-volvo-can?tsmac=store&tsmic=throttle-stop-garage#pid=46&cid=2745&sid=front"]https://teespring.com/en-GB/throttle-stop-garage-volvo-can?tsmac=store&tsmic=throttle-stop-garage#pid=46&cid=2745&sid=front[/url]