The head came back from the machine shop on Friday…apparently set up and ready to go. Well, I've got some ports to finish, so I thought do a little OHC head write up.
Here's the head back from the shop - note that combustion chambers are done BEFORE sending the head in to get the valves cut and the ports are done AFTER as the valve job includes a bowl cut of around 70 degrees that is necessary and better done with a valve seat machine.
Here's the head as delivered.
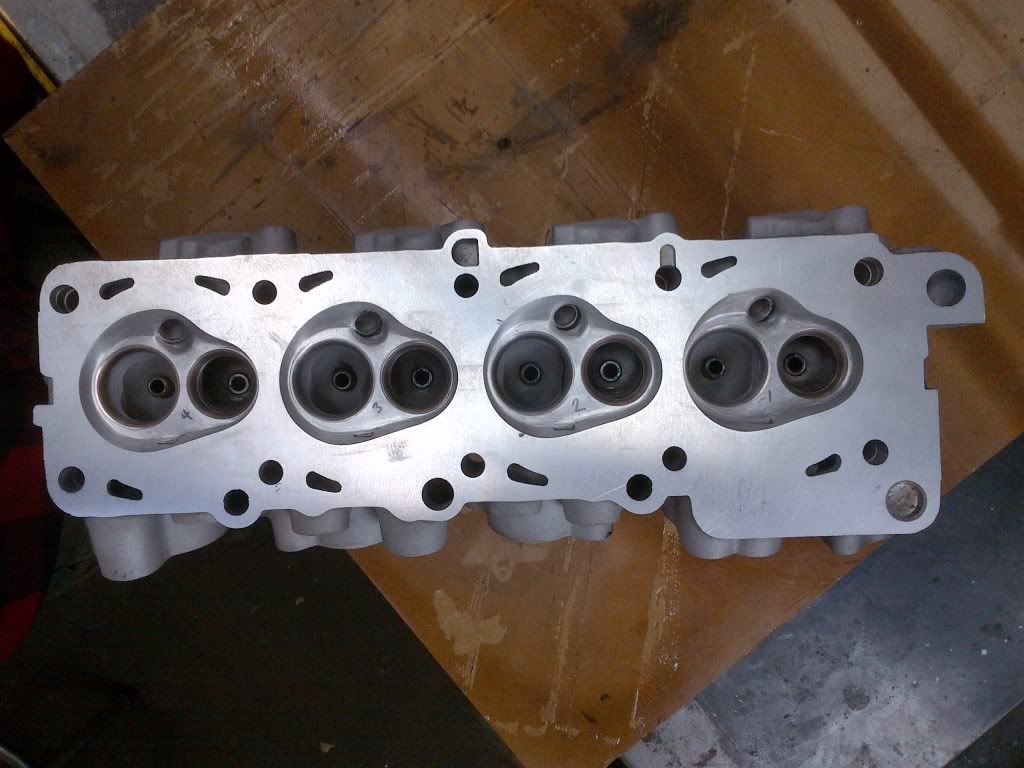
They did a nice job of the seat forms - you can see the three angles and the difference in the seat widths. I'm very happy with this work.
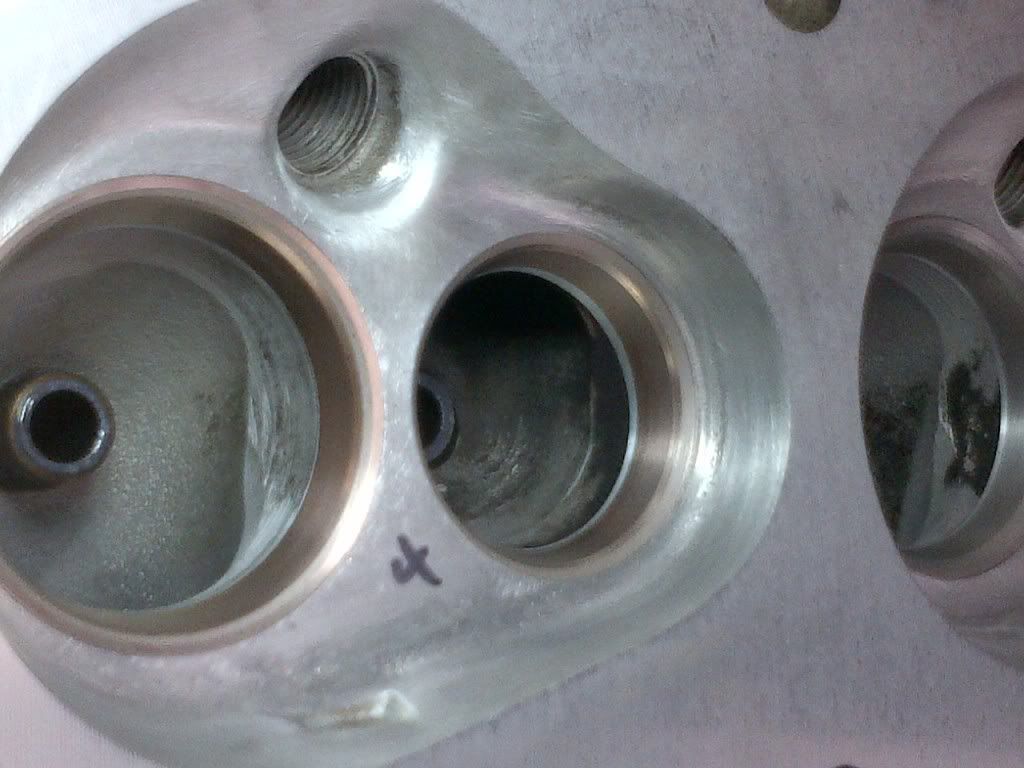
Close-up of the intake seat.
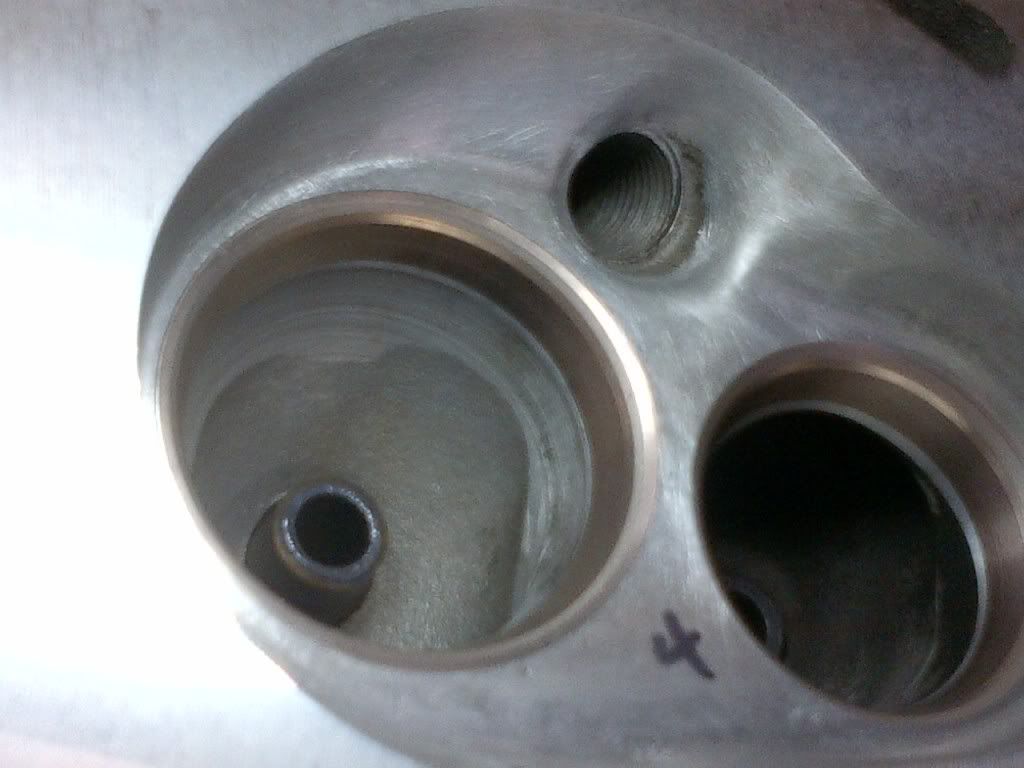
Note all the sharp edges…machine shops don't generally debur the holes - they must be done.
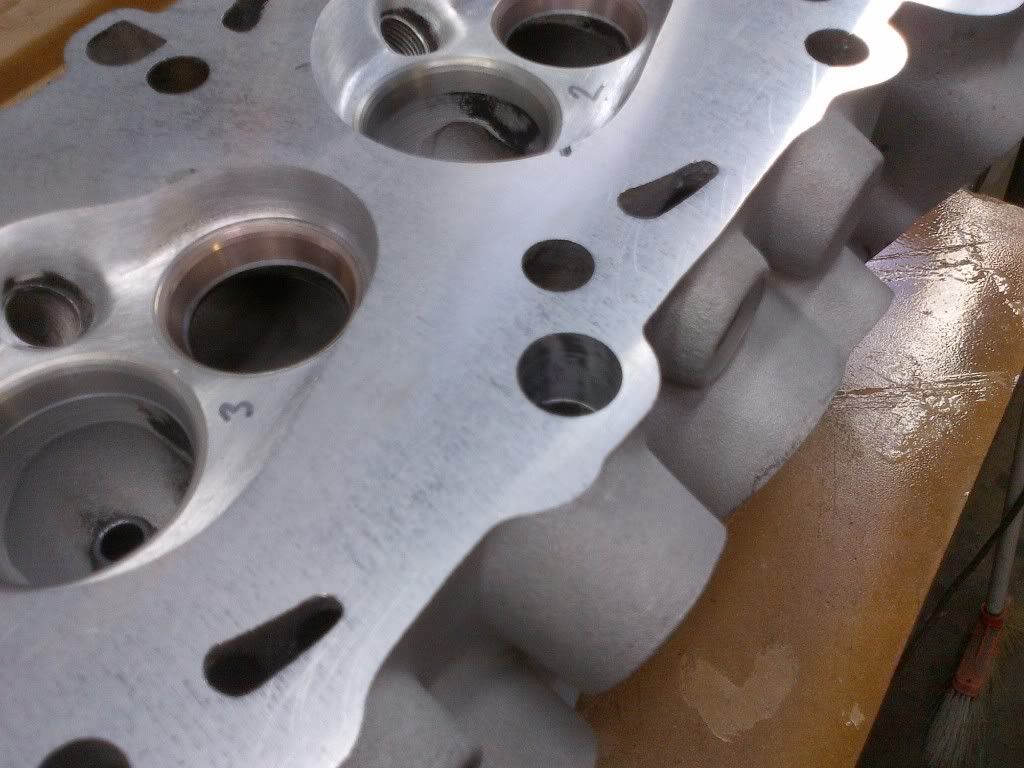
All done. Do all the holes, coolant passages and the combustion chamber. Be very careful.
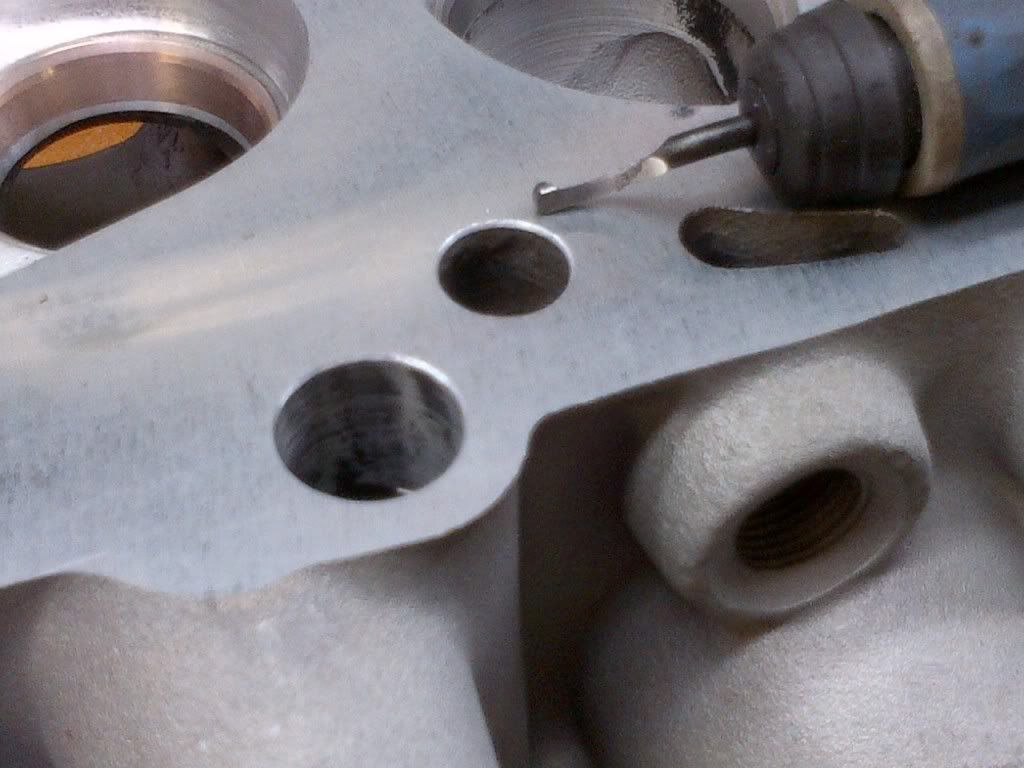
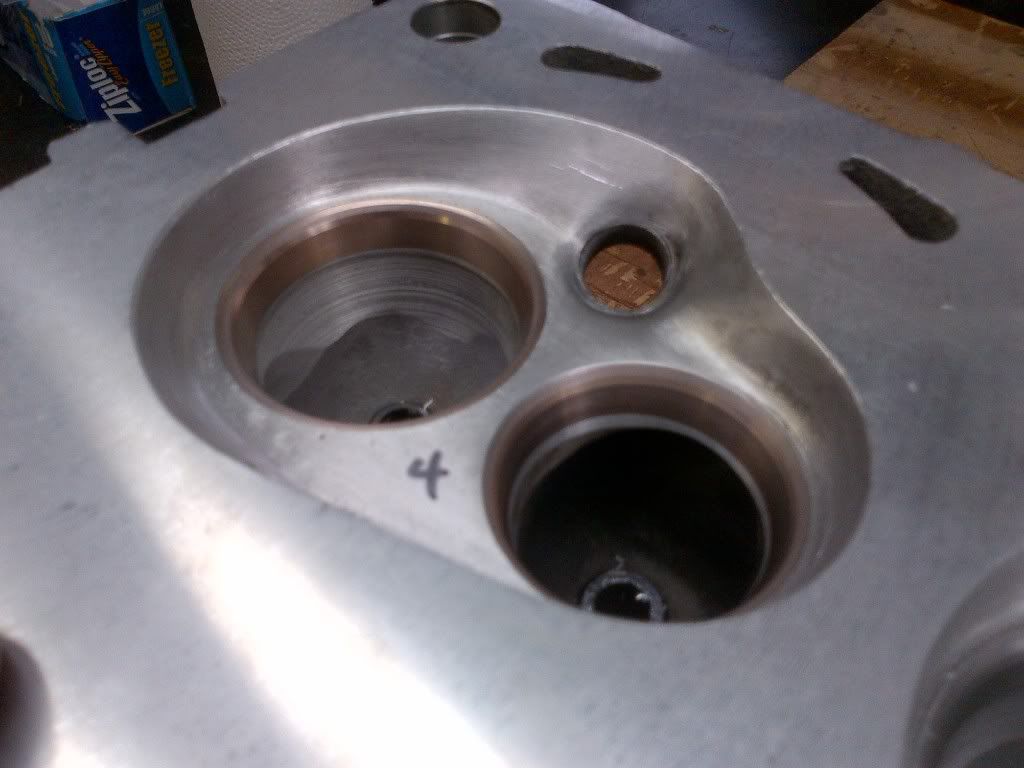
Then tape it up and go to town. The tape is there as a protective barrier against stupid
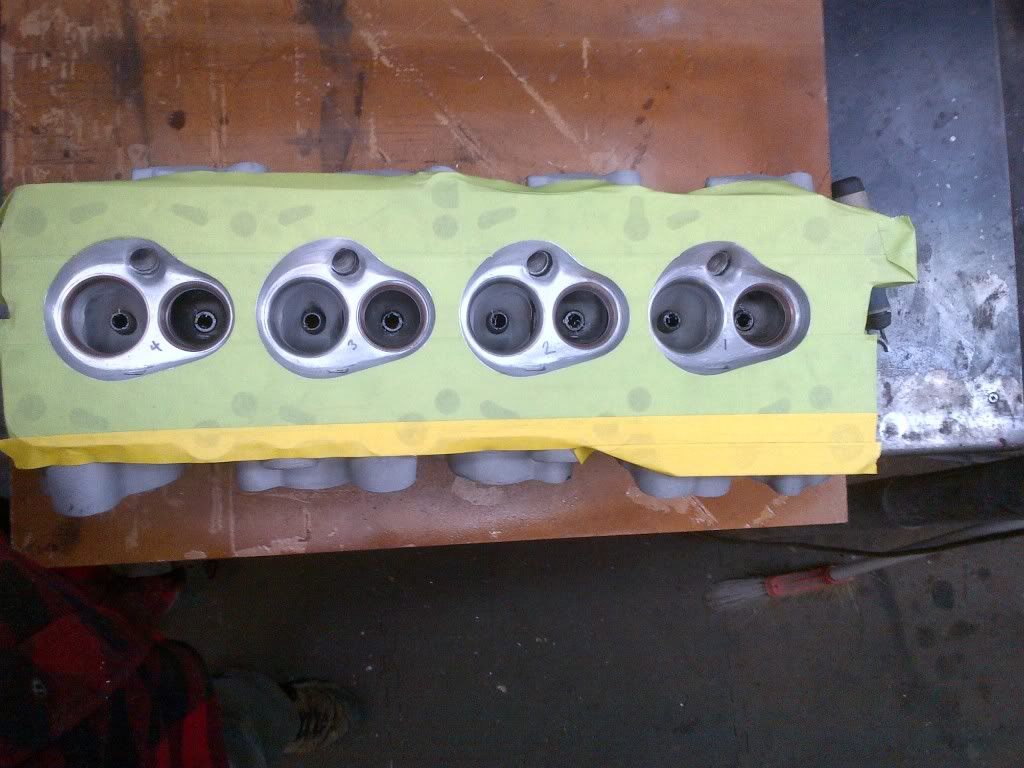
About 8 hours later and we're ready to clean…but first lets have a look.
Intakes gasket matched and finished to 80 grit.
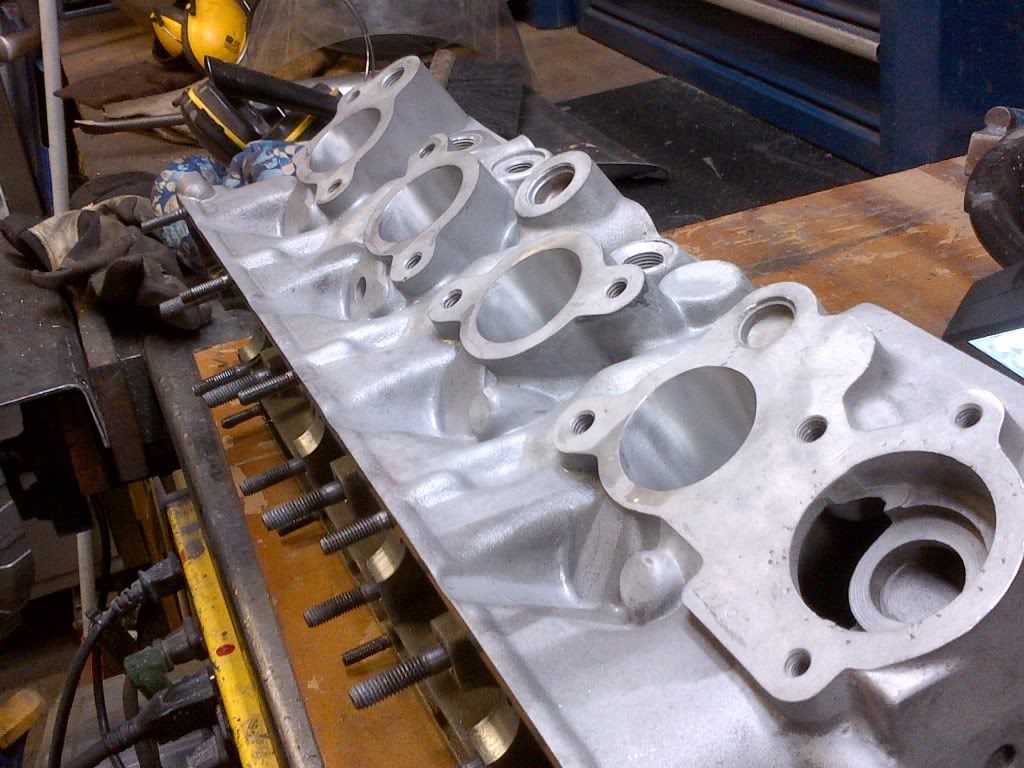
You can see that I blended about half way up the bowl cut on the intake side.
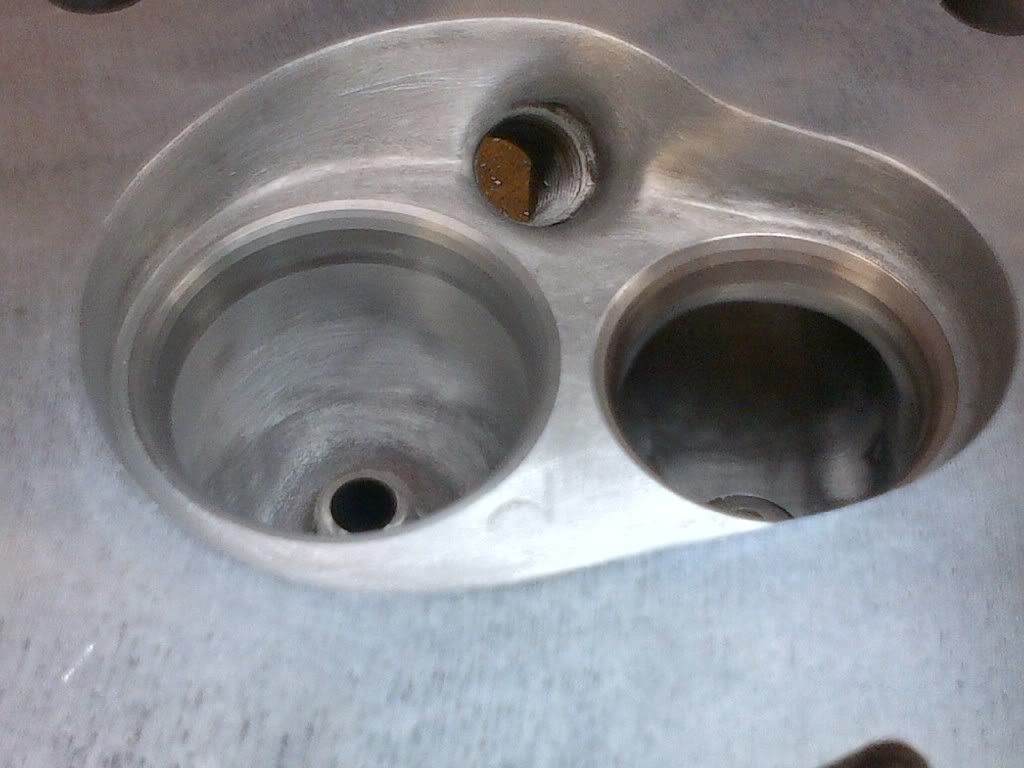
Left the reduction in the port - should work well.
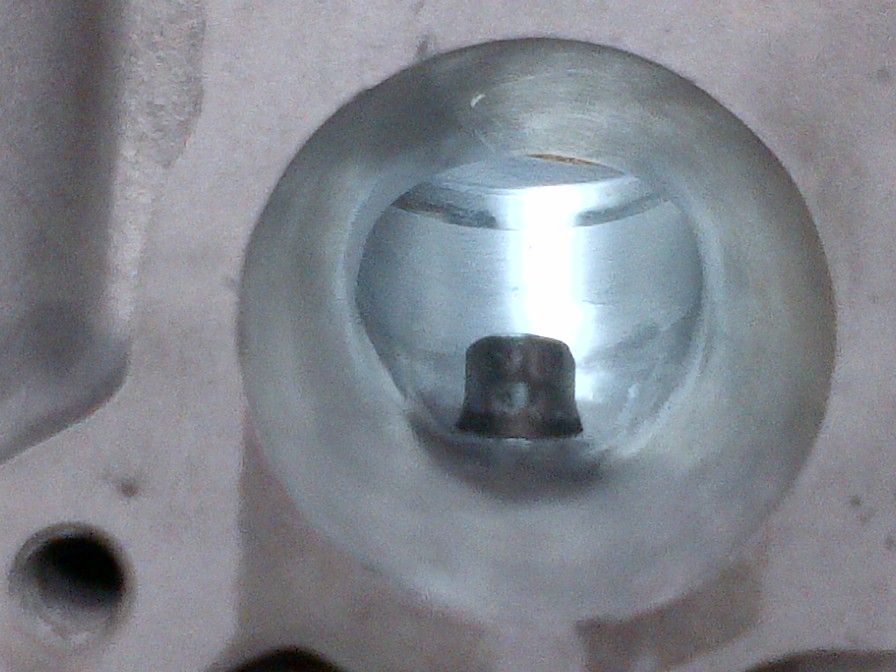
Exhaust side - cut the valve guide level and did the best I could with blending the short-side radius.
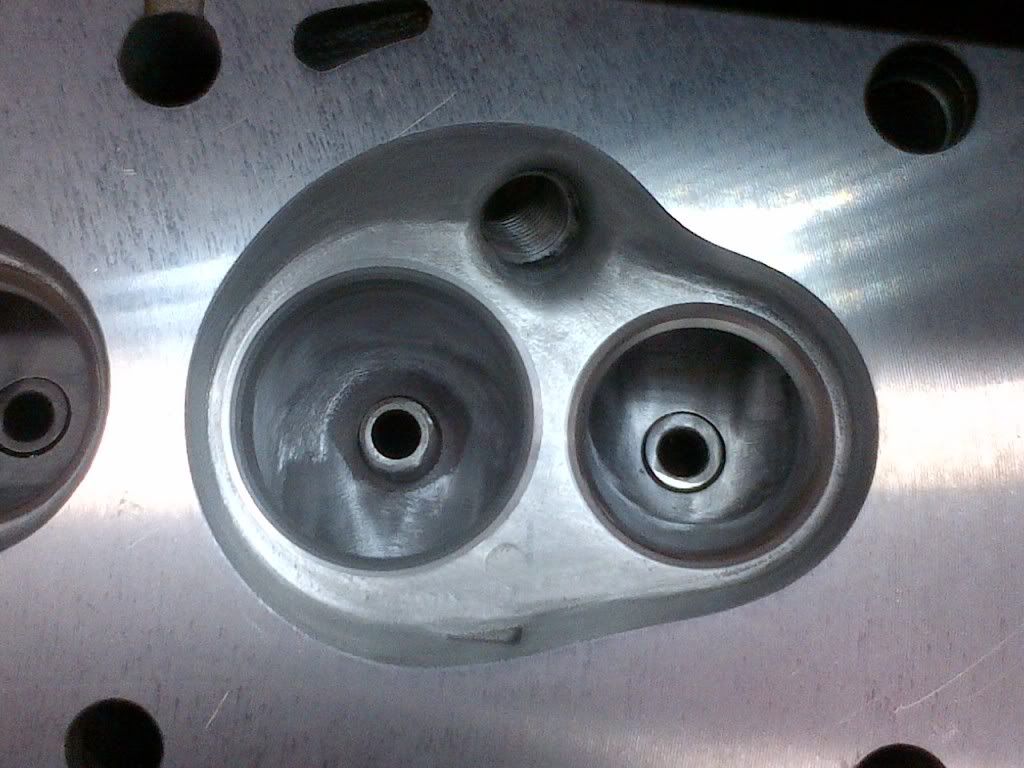
These are not gasket matched to create a little dam that may help with reversion. Port looks pretty nice - finished 120 grit.
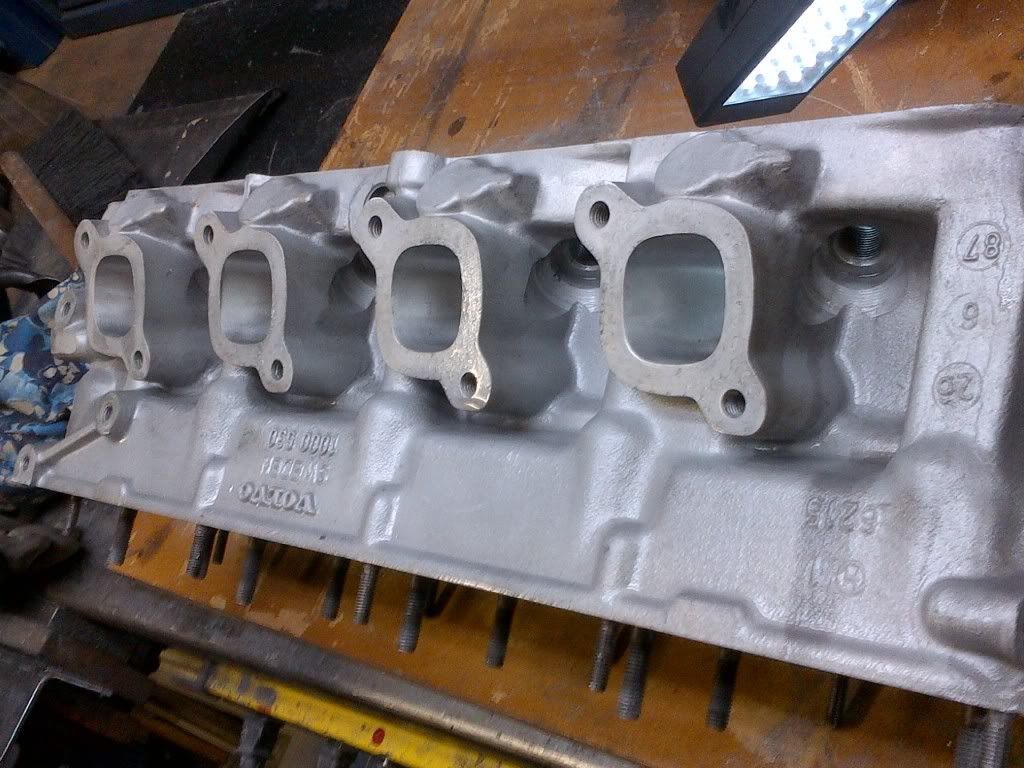
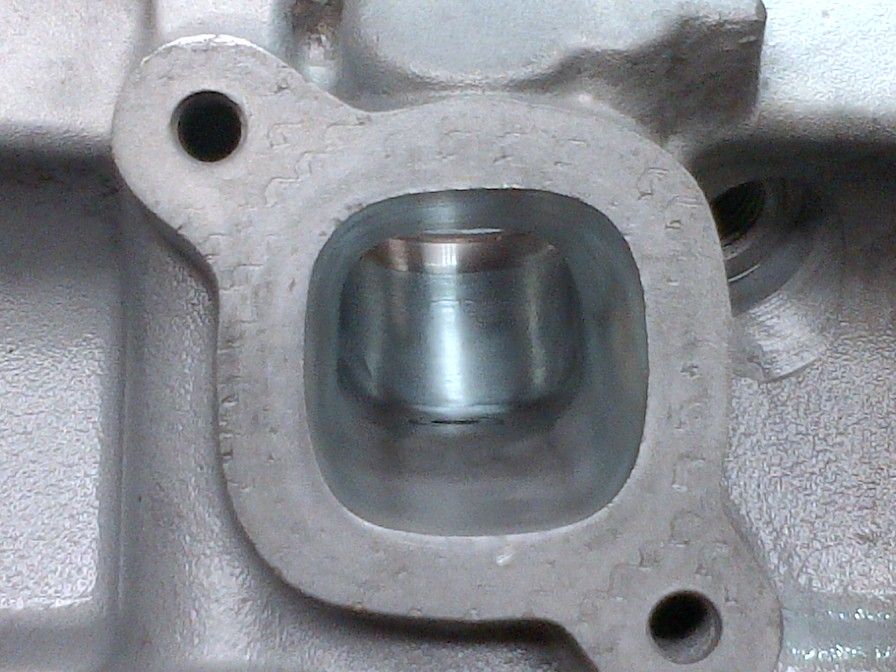
Work the sides of the pocket/bowl area - the gas has to get around the valve and out - help it.
Exhaust valves were back cut and had the head edge radiused for flow.
OK - once done with the pretty stuff, you have to clean. I use bore brushes to clean out the guides.
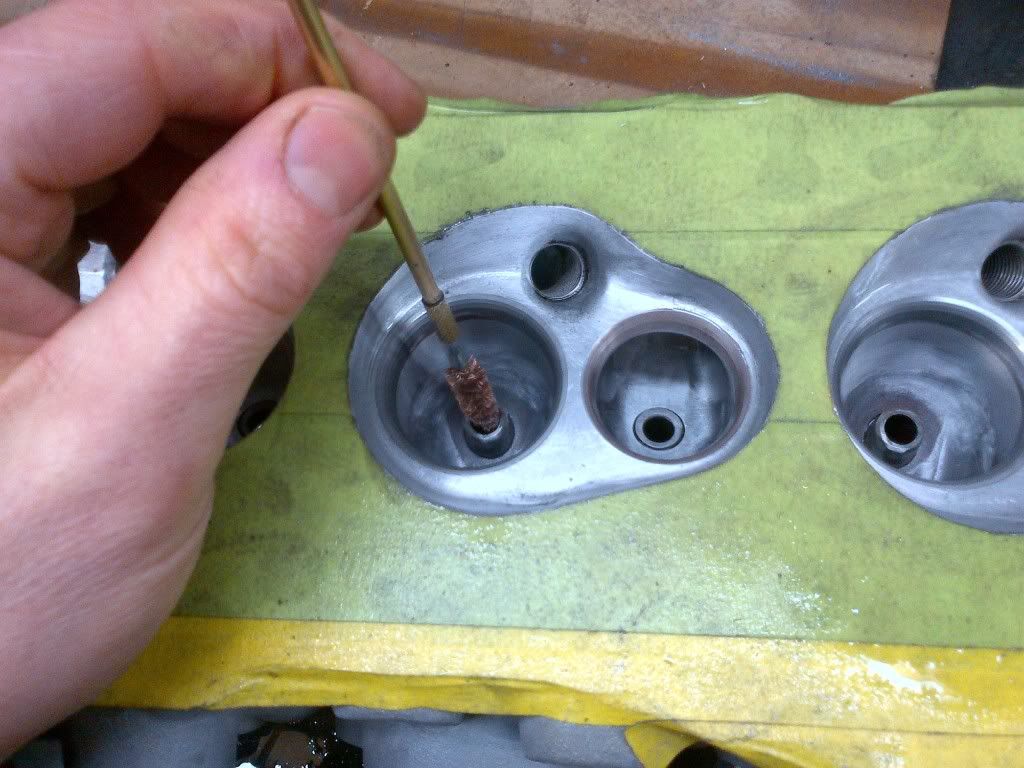
Ready for assembly.
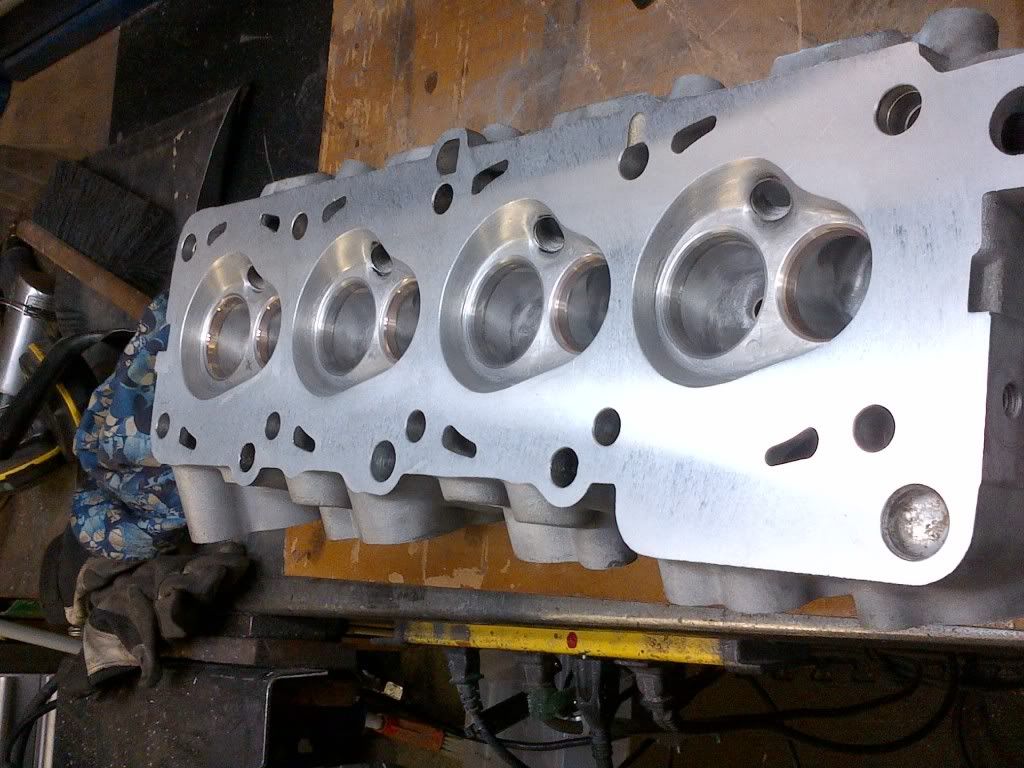
Tools and parts needed. I assemble the springs and keepers but leave the base washers off as they have to go in BEFORE the intake valve guide seals.
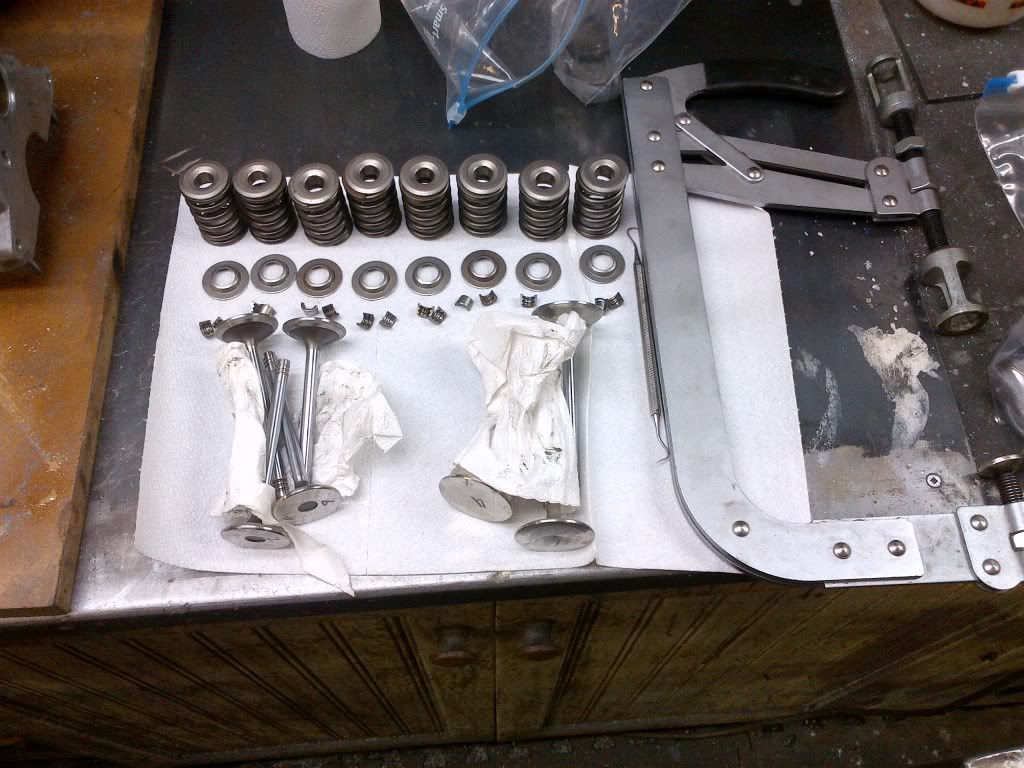
Install the base washers and then pop in the seals. Just push them on with your finger.
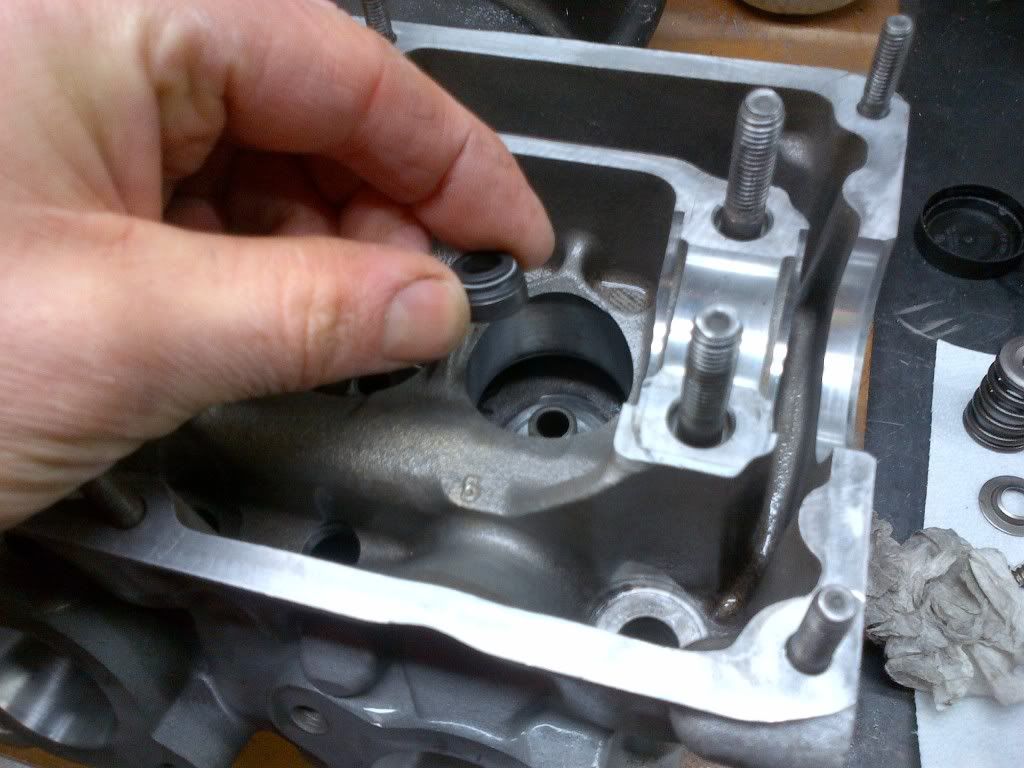
Then coat a valve stem with a little moly grease and insert (it will stay put in defiance of gravity).
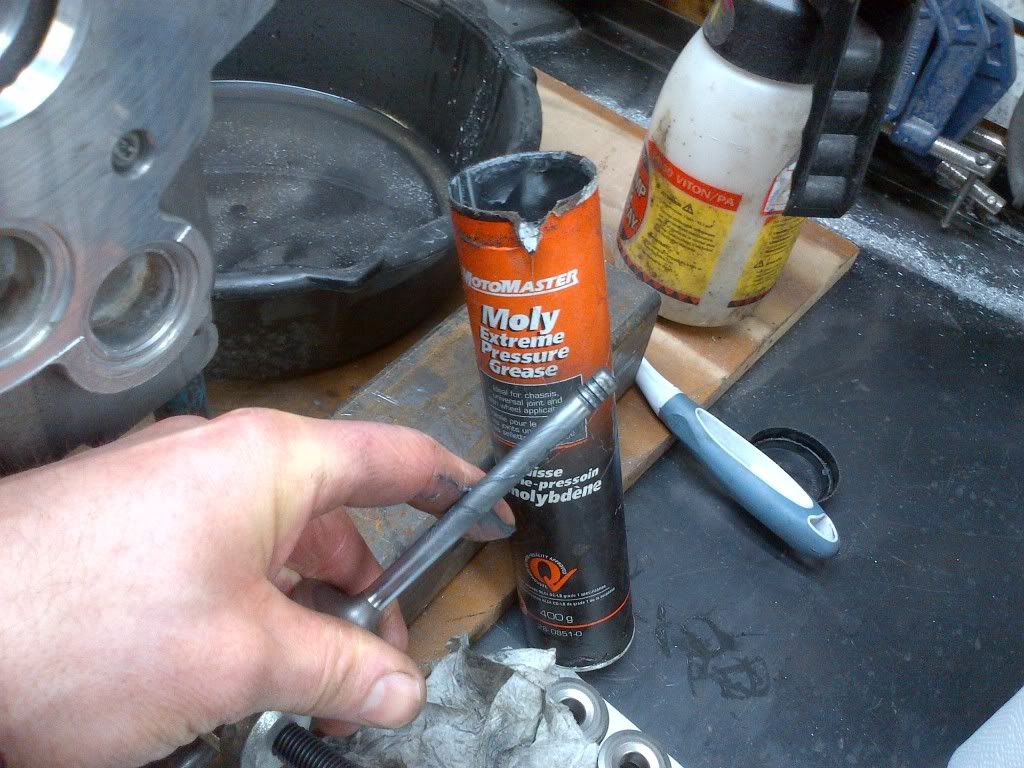
Then load the spring and retainer, snap on the compressor and insert the keepers. A magnetic screw driver is needed for this fiddly job.
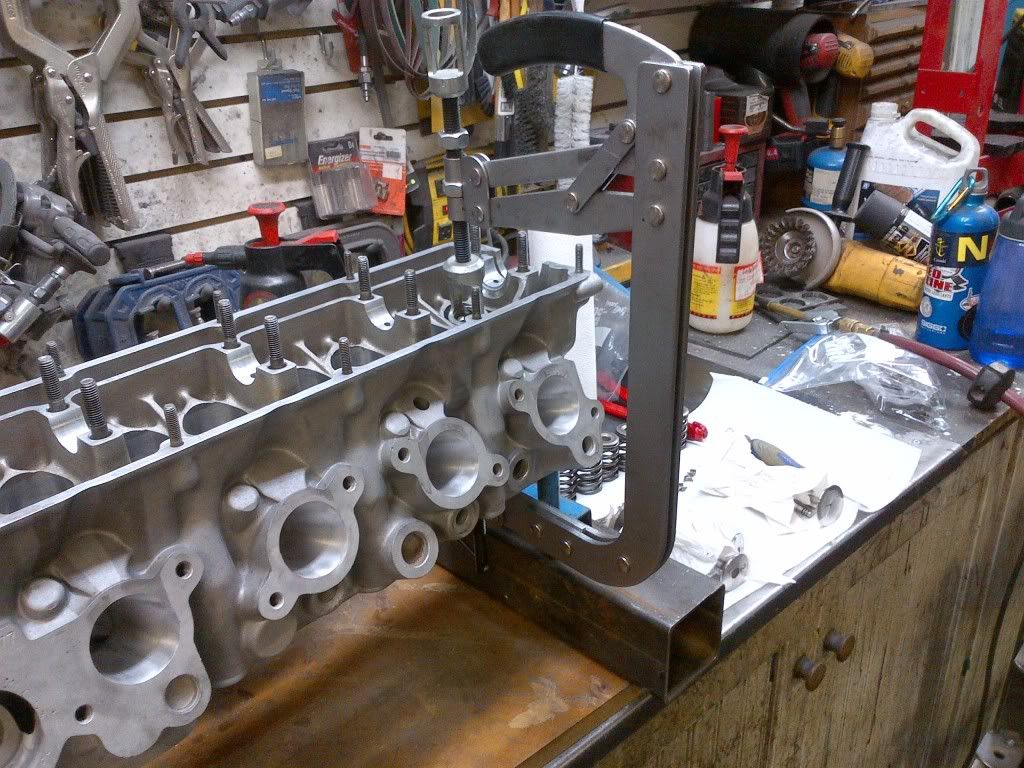
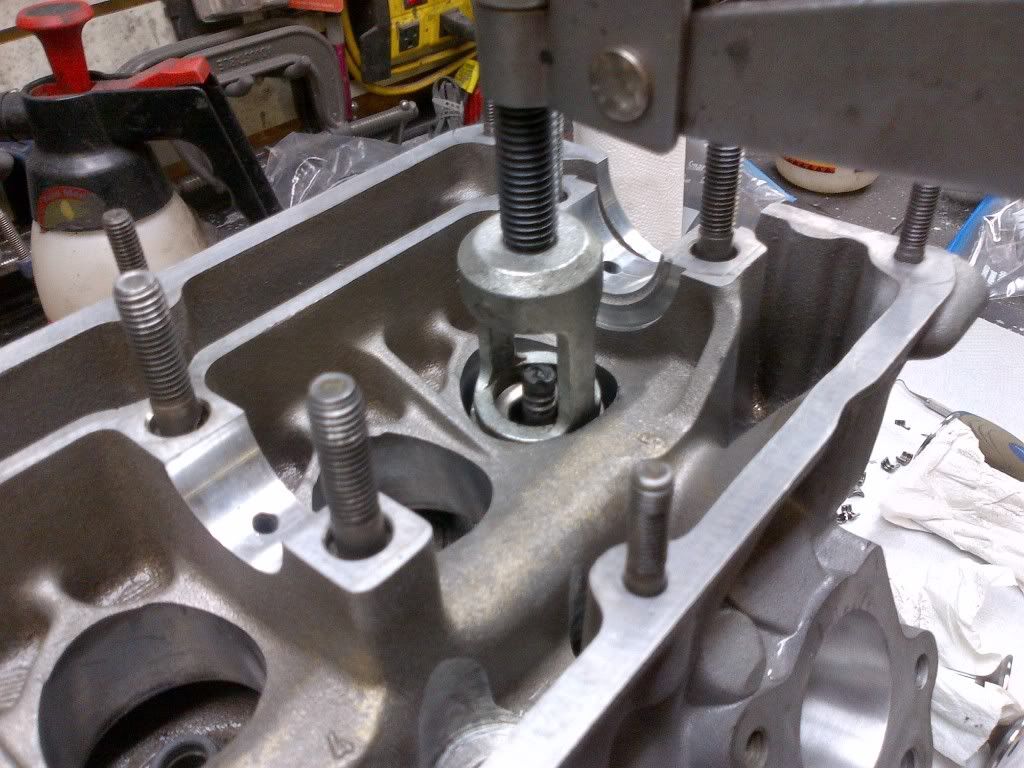
Add the buckets (I oil them first) with the shims. A good squirt of assembly lube and we can test the clearance.
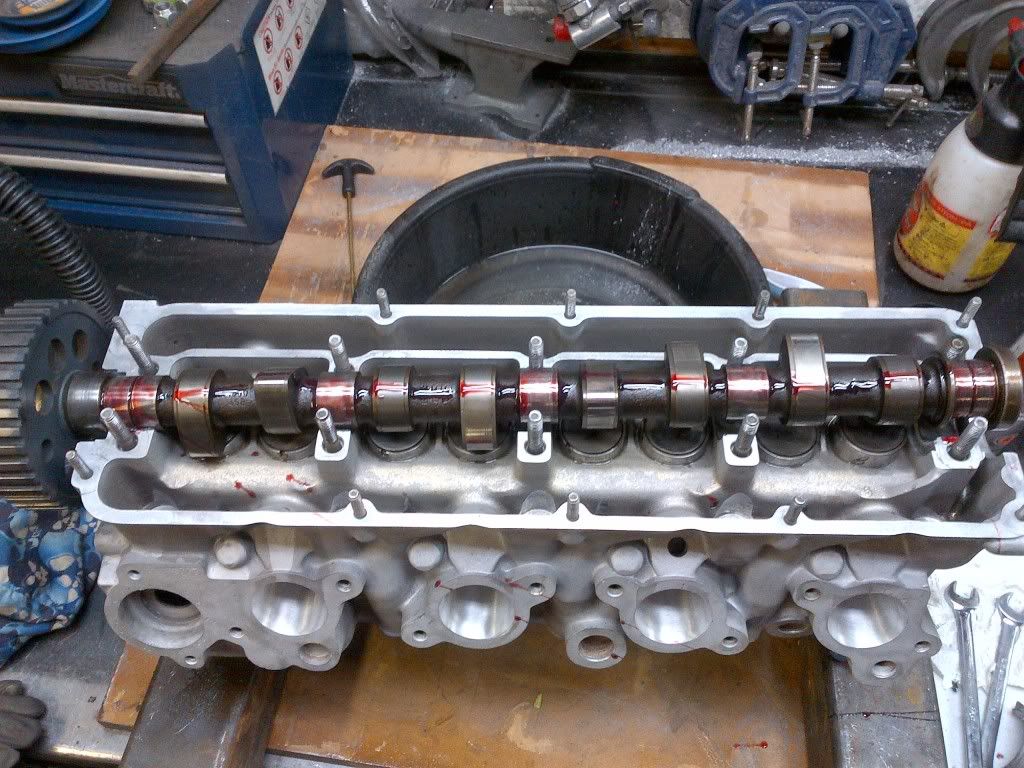
I still haven't found a machine shop that can do this properly…cylinder 1 was fine at 17 thou (should be 18…whatever). All the rest have to be set - WTF. I'll finish it up tomorrow. The valve hushers are installed after the cam is shimmed properly. Always check the machine shops work.