B18/B20 engines are pretty hard on their valvetrain, and one of the components to wear are the rockers. Additionally, the rockers seem to be machined without as much accuracy as one would hope, but they were hammered out in the millions and are something that never seems to fail catastrophically, so I guess you take the bad with the good.
This weekend I tore apart three of my rocker shafts to see what's what, and here's what I found.
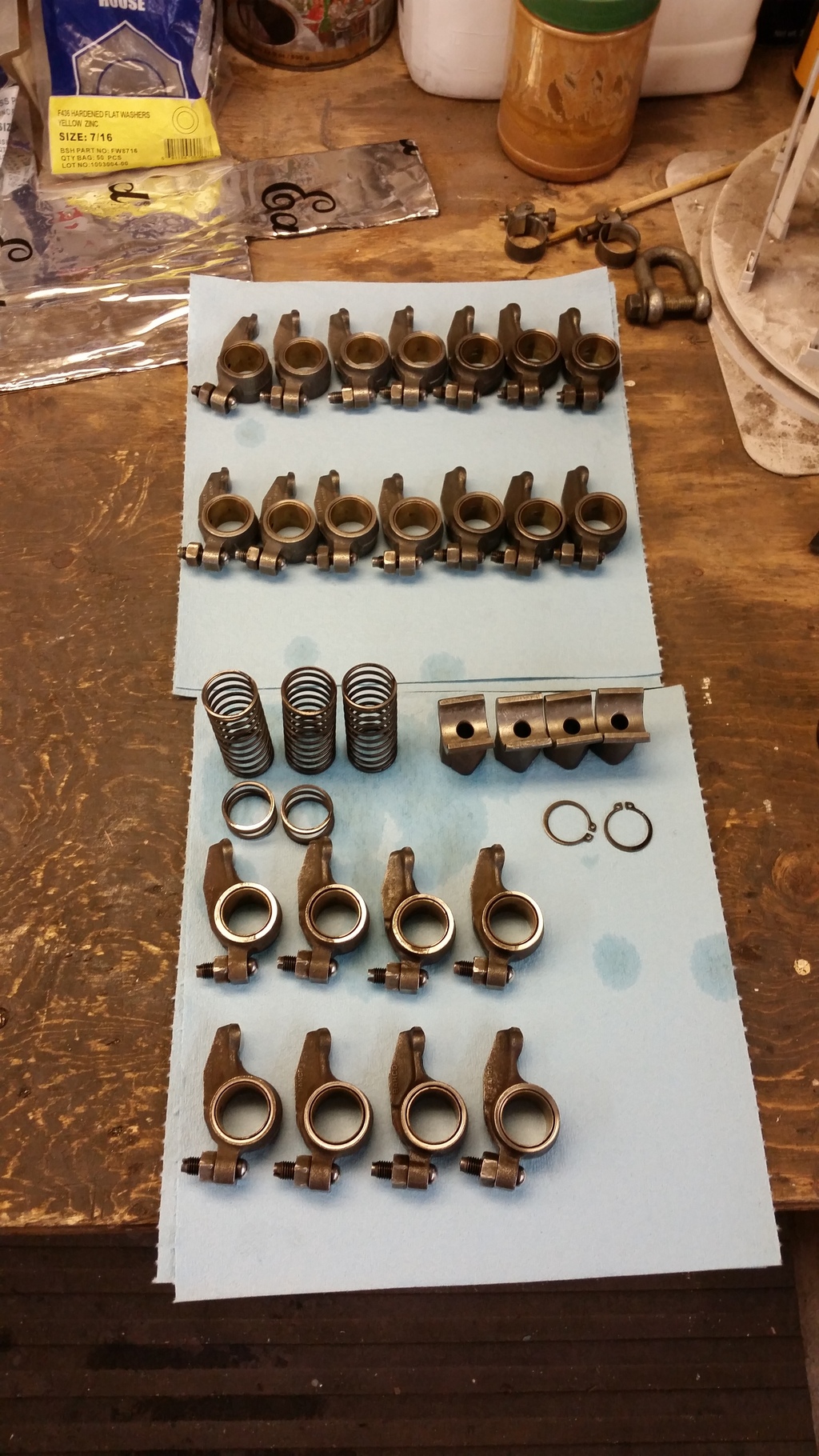
Top left are the rockers from the B18B in my 123GT. Top right are the rockers from a '69 B20. At the bottom are the rockers that came with the B18 I got with the 122. All three sets are different.
The ones from the '67 were exceptionally clean and were in the best shape overall. The bushings were smallest and roundest, and the shaft was in the best shape of the three. They all had a manufacturer's name and a part number forged into them.
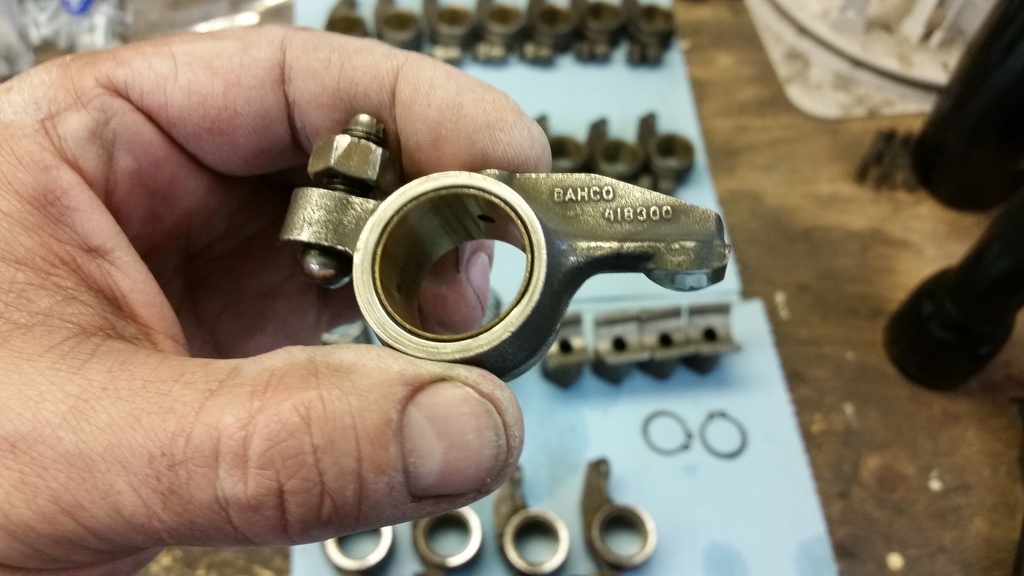
The ones from the '69 were completely without marking, and though they were the same shape overall they also had more meat in some places.
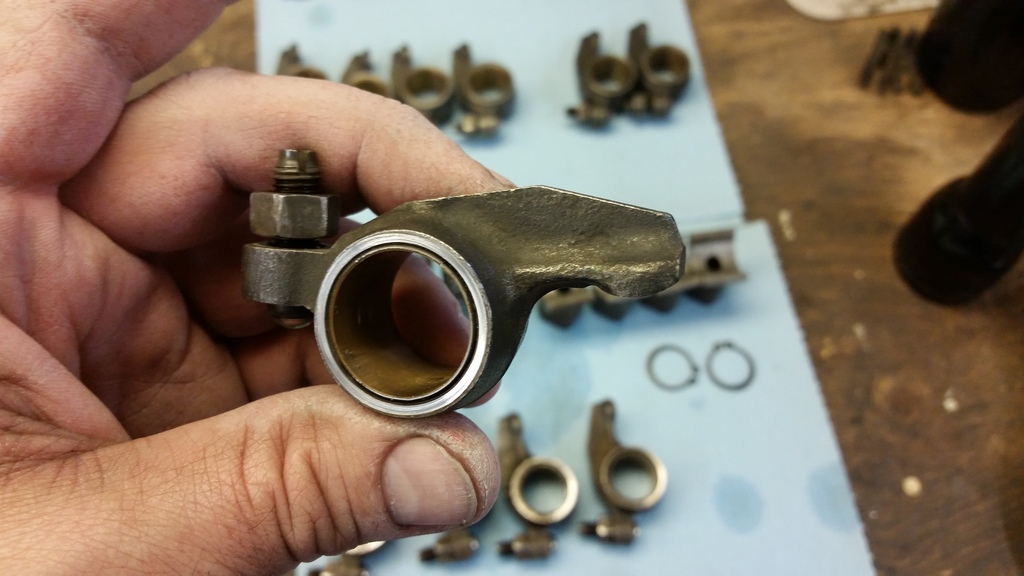
The ones from the older B18 (from a 544, apparently) had the manufacturer name but no part number, and overall looked the same as the ones from the '67 otherwise.
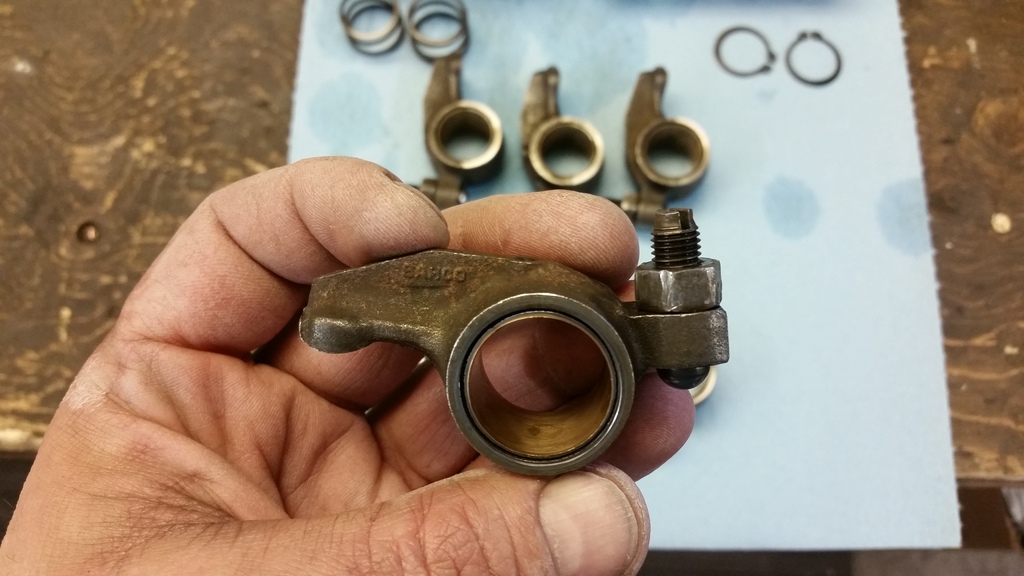
Side-by-each, from the left we have the GT, the earlier B18, and the B20. You can see a wider, flatter forging parting line on the B20 rocker, a wider tip, and a little more beef at the adjuster boss. I'm not saying that ALL B20 rockers are different from B18s, or that they are better or worse, just that there are different styles.
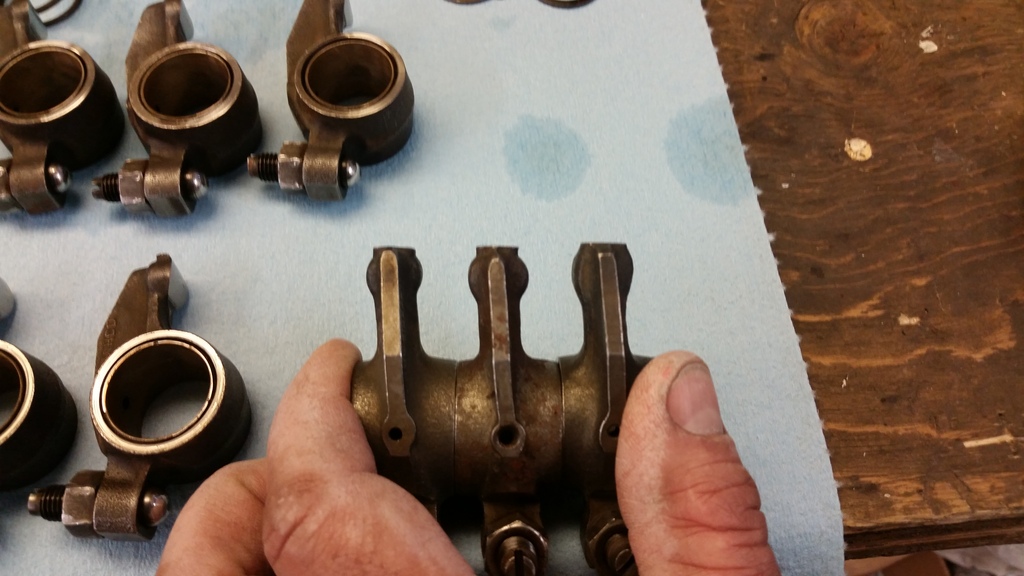
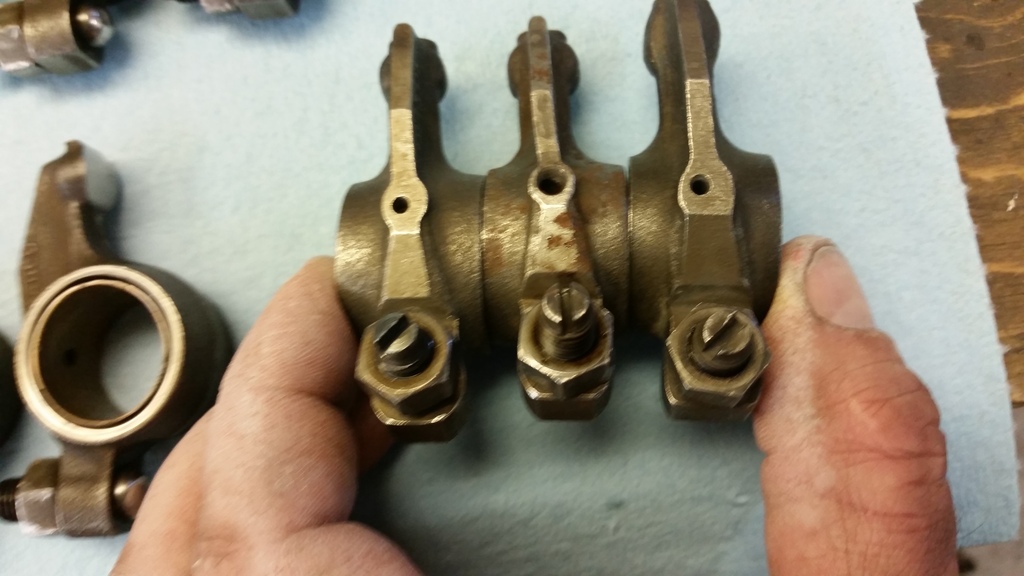
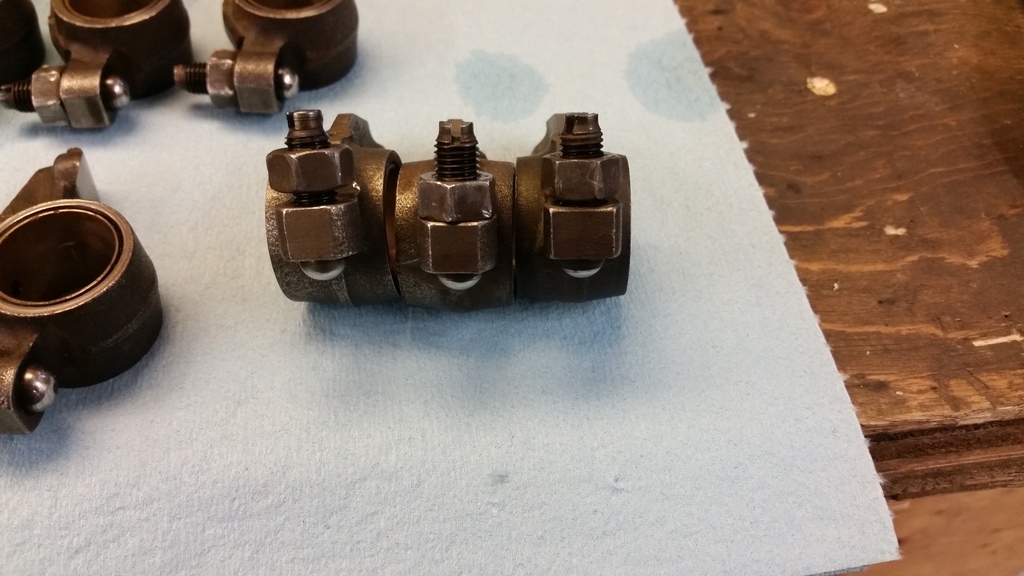
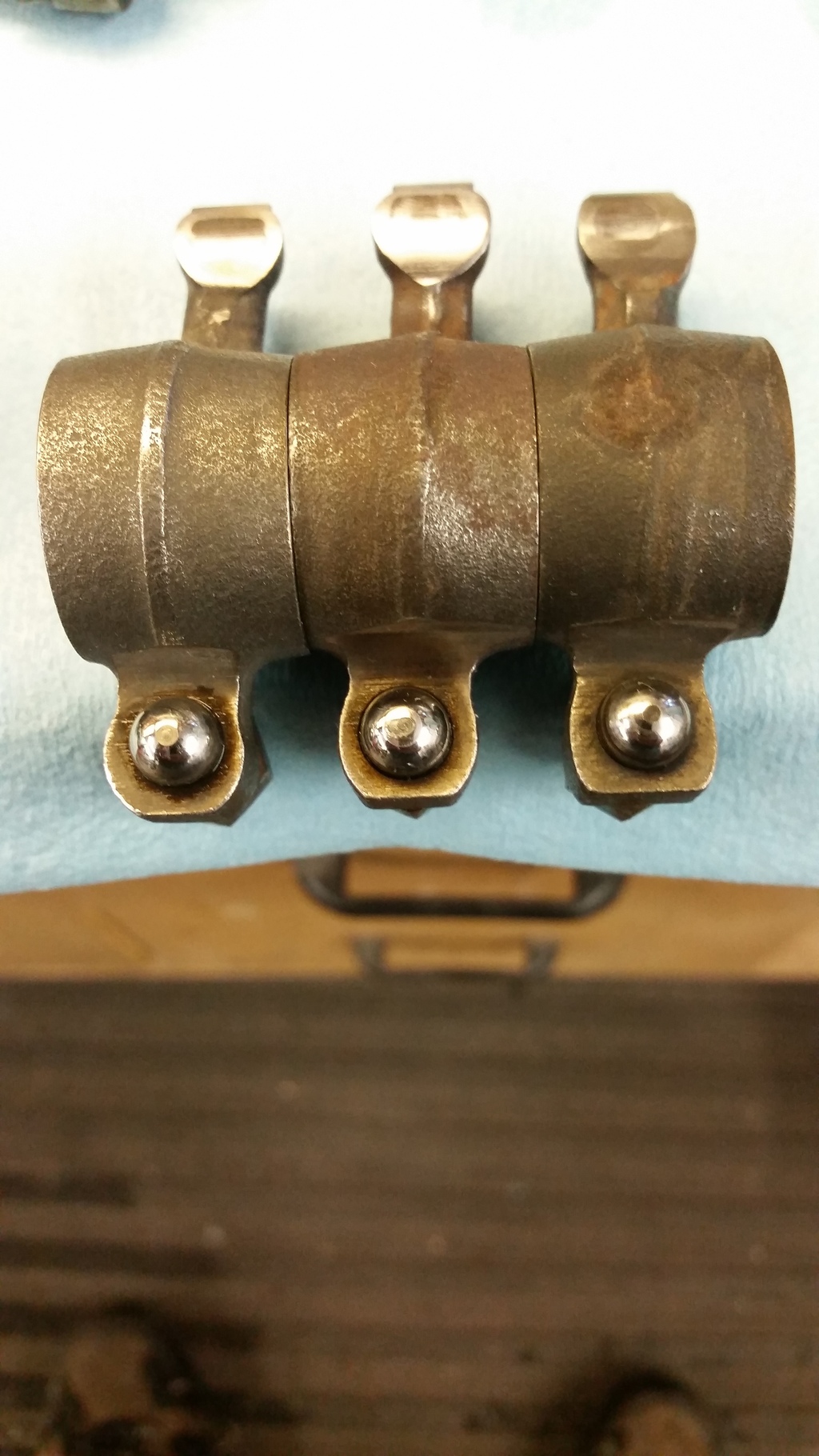
You can also see the typical wear patterns of the rockers at each end. The one in the middle is the one I polished smooth, but didn't reshape. Even after one summer of driving, the wear is evident.
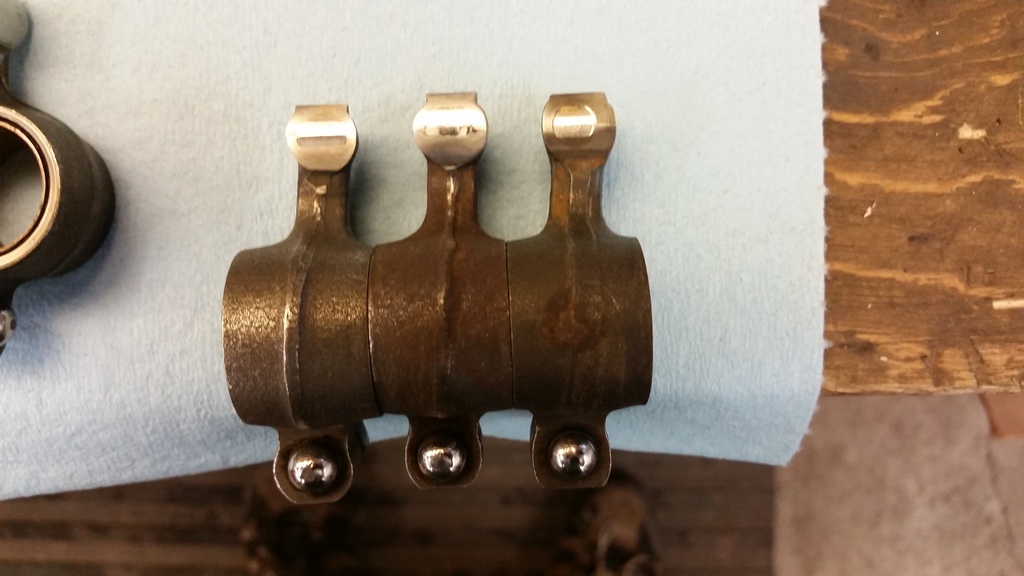
The worn spot on the pad creates troubles in a few ways: The valve can be harder to set properly, the feeler gauge is wider than the worn spot and it doesn't get an accurate measurement of the gap. The worn spot is also not rounded properly to open the valve smoothly, and it's possible that the valve tip and the rocker tip don't meet in exactly the same spot each time, so the rocker may first contact the valve tip on a previously unworn part and then snap into the worn spot, causing noise. Finally, the worn pad contributes to the inaccuracy of the rocker ratio.
To properly refinish this pad, it should be ground with the proper radius, with the axis of that radius parallel to the axis of the rocker shaft, and at the right distance from the rocker shaft. This is quite tricky to do by hand, but without a fixture this is all we can do. In future posts I will show what I have done, and I invite others to show what they've done. I may even attempt to make a fixture to put the right curve in the right place so that they can be done the same way each time. We'll see how that one goes...